Understanding Pipe Volume Calculations A Step-by-Step Guide for Construction Professionals
Understanding Pipe Volume Calculations A Step-by-Step Guide for Construction Professionals - Basic Pipe Volume Formula and Diameter Conversion Methods
Within construction projects, grasping the fundamentals of pipe volume calculations, specifically the formula and diameter conversions, is critical for planning and execution. The core formula for pipe volume is based on the cylinder's volume, utilizing the pipe's radius (\(V = \pi r^2 L\)). Alternatively, the diameter can be directly employed (\(V = \frac{\pi d^2}{4} h\)), potentially simplifying the process. When working with various measurement units, converting diameters from inches to feet – using the factor 0.0833 – ensures accuracy in calculations. Notably, the inner diameter is the key to precise volume determination, and in scenarios where only the outer diameter is known, reference tools like tables can provide estimates of the inner diameter. For professionals in construction, the ability to confidently apply these calculations is indispensable for precise material estimation, capacity assessments, and optimizing system performance. While some might find calculators a simpler approach, developing a foundational understanding of the underlying principles remains vital. The implications of inaccurate volume estimations can range from material waste to inadequate system design, underscoring the importance of accurate and thorough calculations.
1. The foundational equation for determining a pipe's volume relies on the volume of a cylinder formula: \( V = \pi r^2 L \). In this context, \( V \) signifies volume, \( r \) represents the radius (half the diameter), and \( L \) denotes the pipe's length. This seemingly simple formula provides a cornerstone for various engineering calculations. While straightforward, understanding its implications for practical scenarios is paramount.
2. An alternate way to estimate a pipe's volume is using the formula: \( V = \frac{\pi d^2}{4} h \), where \( d \) is the diameter and \( h \) is the length. This slight variation emphasizes the relationship between diameter and the resulting volume. It's important to note that both approaches inherently rely on the geometric principles of cylinders.
3. Converting between units, like changing a pipe's diameter from inches to feet, requires a simple multiplication by 0.0833. It might seem basic, but it becomes essential in situations where various standards or measurement systems are used across projects. Maintaining consistent units is vital to prevent inaccuracies in calculations.
4. Pipe volume calculations primarily rely on the inner diameter since it defines the space available for fluid or material flow. However, scenarios exist where only the outer diameter is accessible, which can complicate matters. In those cases, reliance on reference tables can be necessary to estimate the inner diameter from the outer diameter and the known wall thickness. The accuracy of such estimations will vary depending on the table used and pipe type.
5. Calculating the volume of a pipe isn't just an academic exercise. These calculations are essential for practical reasons, including determining the pipe's capacity. It is relevant for planning fluid storage in various systems or estimating the quantity of materials needed for construction. Accuracy becomes crucial in projects where precise material estimates and resource allocation are paramount.
6. While the formulas are relatively easy to understand, using a specialized pipe volume calculator can be a wise strategy in practice. It's easy to make errors while carrying out manual calculations, and using a calculator minimizes this risk. However, it's always recommended to perform independent checks and verification with independent computations when possible to improve confidence in results.
7. To illustrate, let's consider a hypothetical example: a pipe with a one-inch diameter and a length of 50 feet. By applying the provided formulas, we can easily calculate the volume, which represents the total capacity of the pipe. This serves as a practical demonstration of how the mathematical concept applies to real-world scenarios.
8. The units for expressing pipe volume are cubic units, commonly cubic feet or gallons. Choosing the appropriate unit depends on the context and desired outcome of the calculation. A clear understanding of the application will help determine the ideal unit to avoid confusion and misinterpretations.
9. Professionals in construction and related fields must comprehend pipe volume principles. Accurate estimations of flow rates and storage needs within different systems are essential. This knowledge ensures that systems are appropriately designed and sized, which is a vital aspect of efficient and successful project execution.
10. The ubiquitous mathematical constant \( \pi \) plays a critical role in pipe volume calculations. Understanding that \( \pi \) is an irrational number and understanding its approximate value (3.14159) is fundamental for calculating pipe volumes correctly. While software and calculators can handle the calculation, some basic understanding of the underlying maths remains beneficial for comprehension of the relationships and potential troubleshooting in error analysis.
Understanding Pipe Volume Calculations A Step-by-Step Guide for Construction Professionals - Inner vs Outer Pipe Diameter Measurements for Accurate Results
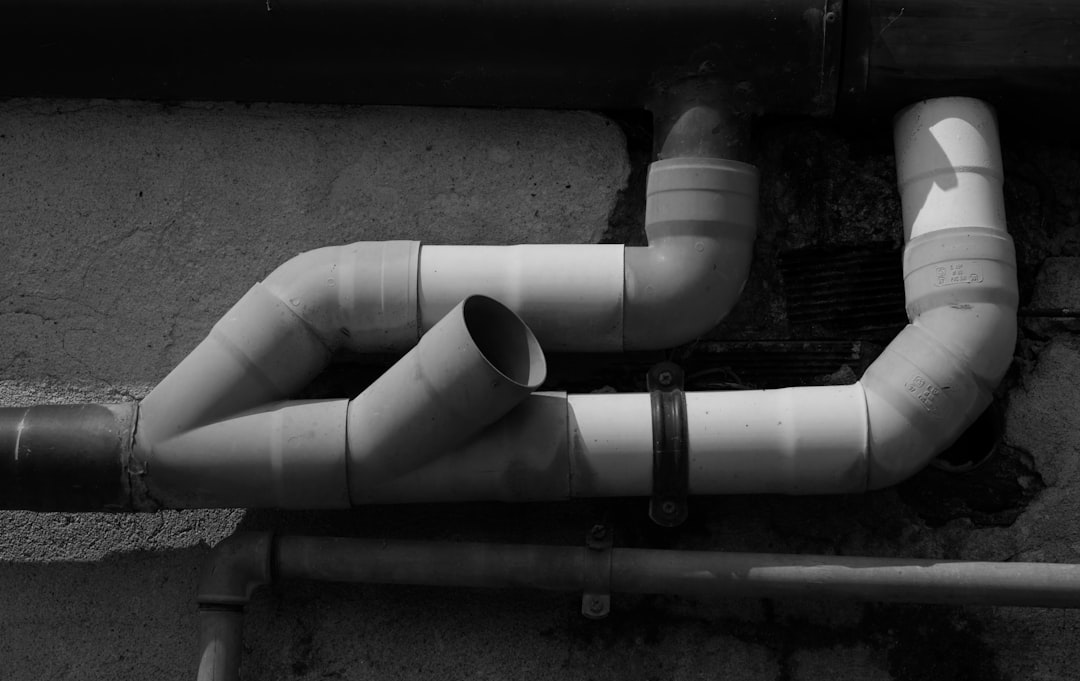
When calculating the volume of a pipe, understanding the difference between inner and outer diameter measurements is critical for accurate results. The inner diameter (ID) directly impacts a pipe's capacity to carry fluids, making it the key measurement for volume calculations related to flow. On the other hand, the outer diameter (OD) primarily influences factors like structural strength and how a pipe fits within a specific space, including its placement during installation.
Getting precise measurements of both inner and outer diameters necessitates the use of appropriate tools like calipers or micrometers. Small errors in these measurements can have a disproportionately large impact on the calculated volume. Moreover, throughout the process, it's crucial to maintain consistent units of measurement (like inches or centimeters) to avoid errors creeping into the calculation.
This careful attention to inner vs. outer diameter and consistent units ultimately leads to more accurate volume calculations. This impacts decisions about material ordering, which in turn improves efficiency and prevents issues in construction projects. In short, a solid understanding of these two measurements helps construction professionals navigate the complexities of pipe volume calculations and achieve more accurate and reliable results.
1. The inner diameter (ID) of a pipe isn't just important for calculating its volume; it's also critical for ensuring flow rates meet design expectations. This is particularly true in systems prone to pressure drops or flow restrictions, where the ID becomes a non-negotiable factor for performance.
2. When comparing the inner and outer diameters (OD), it's vital to understand that variations in wall thickness can significantly impact volume calculations. This means precise measurements are essential, especially in applications with strict capacity limits.
3. One interesting aspect of pipe manufacturing is the variability in wall thickness that can exist even within a single batch. Recognizing these variations is important, as small differences can influence fluid flow and the structural integrity of the pipe.
4. In high-pressure systems, the material properties can change with temperature, which can lead to thermal expansion. This primarily affects the OD, but can indirectly alter the effective ID, making it a concern for engineers designing these systems.
5. The concept of manufacturing tolerances means that a pipe's dimensions can vary slightly from the specified values. Understanding these tolerances is crucial to prevent unforeseen performance problems, especially in fluid transport systems.
6. Both the ID and OD are influenced by the manufacturing process, which introduces variability depending on the method used, whether it's extrusion, welding, or casting. Recognizing how the process can lead to variations allows engineers to make more informed decisions regarding material selection.
7. Sometimes, confusion between ID and OD can lead to errors in calculations, not just for volume but also for the hydraulic characteristics of a system. This emphasizes the need for clear documentation and communication between engineering teams.
8. The distinction between the nominal and actual dimensions, often defined by industry standards, necessitates verification using tools like calipers or micrometers. Relying solely on nominal values stated in specifications can lead to inaccurate results.
9. In some applications, the ID can be affected by factors like corrosion or scaling over time, potentially reducing the effective flow area. Regular inspections and measurements throughout a pipe's lifespan are important to ensure continued optimal performance.
10. Understanding the implications of inner and outer diameters extends beyond simple volume calculations. These dimensions directly impact critical factors like stress distribution and failure analysis, highlighting the non-trivial importance of accurate measurements in construction applications.
Understanding Pipe Volume Calculations A Step-by-Step Guide for Construction Professionals - Real World Applications in Municipal Water Systems
Within the context of municipal water systems, understanding pipe volume calculations becomes paramount for effectively managing water supply and planning infrastructure. Accurately calculating the volume of pipes ensures that water distribution systems can consistently deliver the necessary amount of water to meet demand, mitigating potential issues arising from insufficient capacity or excessive pressure loss.
Beyond simple capacity estimations, a thorough grasp of factors impacting water flow through pipes, such as diameter and material type, is crucial. These insights inform design decisions during both construction and maintenance projects. For instance, considering how different materials affect water flow rates helps to ensure that designs optimize hydraulic efficiency.
The importance of comprehending pipe volume calculations extends to accurate material estimations. Construction projects relying on such estimations can avoid over- or under-ordering, thereby minimizing waste and contributing to cost-effective resource management. Furthermore, properly designed and sized systems, based on accurate calculations, become integral to achieving a reliable and efficient municipal water supply system, ensuring the consistent delivery of a vital resource to the community. This critical understanding of pipe volume translates to informed decisions that ultimately contribute to the overall effectiveness of water management within a municipality.
1. In the design of municipal water systems, engineers frequently rely on sophisticated software that simulates how water flows through the network of pipes. These programs consider things like friction within the pipes and how pressure changes, allowing engineers to make better design decisions and spot potential problems before construction starts. This is important because it can avoid costly repairs and delays later on.
2. The state of the inside surface of pipes in a municipal water system is directly related to how old the system is. Over time, things like corrosion can erode the inside of the pipe, effectively making it narrower and causing more resistance to the flow of water. This reduces the amount of water that can flow through it, and means that regular inspections and maintenance are necessary to keep things operating well.
3. The material a pipe is made from can significantly impact how water flows through it. For example, PVC pipes usually have a smoother surface compared to metal pipes, resulting in less friction and better flow rates. Understanding these material-specific differences is essential when designing a system and ensuring that water can be efficiently delivered.
4. Water distribution systems often utilize a variety of pipe diameters to efficiently manage water pressure. Larger pipes are generally used for main water lines, minimizing pressure drops over long distances. Conversely, smaller pipes are often adequate for distributing water to individual homes.
5. The maximum pressure a pipe can withstand before it fails depends not only on the material it's made from but also on the temperature of the water flowing through it. High temperatures can weaken pipe materials, making them more susceptible to pressure-related failures. Selecting the right pipe material for specific operating conditions is therefore a crucial consideration to ensure long-term system reliability.
6. When determining how much water a municipal system needs to store and transport, engineers must account for periods of high water demand. This includes things like seasonal variations where water usage can spike, requiring careful adjustments to pipe sizing to prevent water shortages. Predicting these usage patterns is a vital part of planning these systems.
7. Modern water distribution systems frequently incorporate advanced methods to detect leaks. Techniques like acoustic monitoring can detect variations in sound that signal a leak, allowing for quick repairs and minimizing water loss. This approach reduces waste and can potentially improve the efficiency of the system.
8. Fluctuations in water pressure can cause pipes to burst, especially older pipes that become brittle over time. Understanding the connections between water pressure, temperature, and the material of a pipe is essential to avoid failures that can lead to disruptions in service.
9. Municipal engineers must be conscious of a phenomenon called "water hammer," which happens when the flow of water is suddenly stopped or redirected. This sudden change in momentum can generate damaging pressure waves that can harm pipes and components of the system. Careful design practices, including careful pipe layouts and mechanisms to release excess pressure, can mitigate the effects of water hammer and ensure system integrity.
10. The method used to join sections of pipe together can have a major effect on the installation process and long-term reliability. Techniques like fusion welding and solvent cementing offer advantages like minimizing leaks and ensuring a strong connection. Engineers should consider these factors when designing systems, to achieve the best performance possible.
Understanding Pipe Volume Calculations A Step-by-Step Guide for Construction Professionals - Standard Industry Tables and Reference Materials
When dealing with pipe volume calculations, relying on established industry tables and reference guides is incredibly helpful for construction professionals. These resources are packed with essential formulas, practical advice, and helpful charts that make it easier to estimate pipe volumes and select the correct materials. Textbooks like the "Piping and Pipeline Calculations Manual" are particularly useful because they don't just focus on the math of volume calculations, but they also provide information on important industry codes and standards, which is crucial for making sure projects comply with regulations. Since piping systems can get quite intricate, using these materials can help professionals approach design issues with better accuracy, improving their decisions when planning and carrying out a project. It's very important that professionals stay up-to-date on the most recent industry standards to make sure their construction projects are successful. Without access to the current information, errors and issues can occur in any part of a project.
1. Industry standard tables and reference materials offer a wealth of pipe dimension data, often derived from rigorous testing and adhering to established standards. This ensures engineers have access to dependable measurements crucial for accurate calculations, particularly in the realm of fluid dynamics. While valuable, it's always important to critically examine the origins of the data.
2. Beyond just nominal sizes, most of these resources will also detail wall thicknesses and material types, enabling engineers to factor in the complexities of practical applications. This is especially useful when dealing with pressure ratings and aspects like thermal expansion, which can impact calculations. Depending on the specific application, different material properties can influence the design and performance.
3. Historical data on pipe materials and their performance under various conditions can often be found within these tables. This information allows engineers to make more informed predictions regarding long-term durability and reliability across different environments. However, the accuracy of these predictions relies on how well historical data aligns with current practices and materials.
4. It's intriguing to note that even pipes manufactured to the same nominal diameter can exhibit surprising variations. The existence of manufacturing tolerances means that actual dimensions can differ, which can significantly influence calculations if not accounted for properly. While these variances might seem minor, they can impact performance, especially in systems with tight tolerances.
5. Many reference tables conveniently include conversion factors for standard units of measurement, enabling engineers to quickly convert between units without laborious manual calculations. This ease of use can save time, but it's important to remember that reliance solely on conversion factors without understanding the underlying principles can create challenges.
6. It's crucial to fully understand the source and methods used to create the tables. Some tables might stem from empirical data, while others rely on computational fluid dynamics simulations. This emphasizes the importance of applying the right context when interpreting the information, ensuring the approach aligns with the engineering challenge.
7. Pipe geometry isn't limited to perfect cylinders in real-world situations. Reference materials often factor in the intricacies of flanges, fittings, and joint types, which can affect flow dynamics and overall system efficiency. While these details are important, accurately incorporating them into calculations can sometimes pose challenges.
8. Some of these resources provide standardized coefficients for surface roughness. This is particularly valuable when determining friction losses in a pipeline system, highlighting the comprehensive approach necessary for accurate calculations in fluid mechanics. However, it's important to recognize the limitations of standard coefficients and understand their applicability to different flow regimes.
9. It's fascinating how even minor temperature changes can affect material properties. Standard tables frequently incorporate thermal expansion coefficients to aid engineers in assessing the potential impact of temperature variations on pipe integrity and performance. It's always important to ensure that the thermal properties used are accurate for the intended operating conditions.
10. While digital databases are gaining popularity, printed industry tables haven't lost their significance. They serve as a quick reference point, especially in field conditions where accessing digital resources might be challenging. This provides engineers with a backup method for accessing key data but reinforces the idea of a multi-faceted approach to data access.
Understanding Pipe Volume Calculations A Step-by-Step Guide for Construction Professionals - Calculating Flow Rates and System Capacity
Within the broader context of pipe volume calculations, understanding "Calculating Flow Rates and System Capacity" is vital for designing and operating efficient systems. This involves connecting the physical dimensions of a pipe to the movement of fluids within it. At the heart of this concept is the relationship between the pipe's cross-sectional area and the velocity of the fluid moving through it. This understanding is crucial for determining if a pipe or a system of pipes has the ability to handle the intended flow of materials.
To estimate a system's capacity, we need accurate calculations, using formulas that relate the cross-sectional area of the pipe and the speed of the fluid. For instance, calculating the volumetric flow rate – the volume of a fluid moving through a point in a given timeframe – employs a basic formula: \(Q = A \times v\). While seemingly simple, this highlights how pipe diameter and material influence a system's capacity. Moreover, tools like the Hazen-Williams equation are used to figure out the velocity of the fluid in the pipe, illustrating the importance of precise measurements to ensure system performance across a variety of contexts, like water systems or drainage networks.
It's important to recognize that any errors or inaccuracies in these calculations can lead to practical problems. These errors can range from a system being undersized for its intended purpose to creating issues like pressure drops or flow restrictions. Consequently, developing a comprehensive understanding of how to accurately calculate flow rates and system capacity is crucial for success in various construction projects.
1. Calculating flow rates often involves more than just pipe diameter; factors like the fluid's thickness (viscosity) and temperature play a significant role. For example, a thicker fluid will resist flow more than a thinner one, showing that simple diameter calculations are insufficient in many real-world situations.
2. In intricate pipe networks, the actual capacity can be influenced by bends and connections. Each bend adds friction, altering the flow, so engineers need to consider all parts when estimating capacity to avoid unforeseen performance issues. It seems that simplistic models might not be accurate in representing real-world systems with these kinds of complexities.
3. Even minor differences in pipe diameter caused by manufacturing can lead to notable differences in flow rate calculations. A slight difference of just 1/16th of an inch over a long stretch of pipe could lead to unexpected pressure drops, emphasizing the importance of close attention to detail in design.
4. The Darcy-Weisbach equation, a widely-used tool for engineers to calculate pressure loss, considers factors like pipe diameter, length, flow rate, and the fluid's density. This highlights that effective flow rate estimation needs to incorporate the principles of fluid dynamics rather than only relying on simple volume calculations. In other words, the physics of fluids needs to be considered as well.
5. Interesting engineering solutions can stem from recognizing that pipe design isn't just about dimensions. For example, incorporating tapered sections or optimizing the layout can improve flow rates. It seems we need a more comprehensive approach to design that moves beyond the most basic calculations.
6. The continuity equation, which states that the mass flow rate remains constant even when pipes change diameter, is fundamental to flow rate calculations. Engineers can leverage this principle to create systems that handle changes in usage efficiently without compromising performance. It's interesting how the physical laws of fluid flow can be used for engineering design.
7. Calculating flow rate accurately can improve system robustness. For example, precise calculations can help engineers incorporate redundancy into municipal water systems, creating alternative paths if a main line fails, increasing reliability. This shows that the calculations can have a positive impact on the performance of engineering designs.
8. Understanding the relationship between flow rate and pressure loss is crucial for pumping systems. Too much pressure loss from poor design or inaccurate calculations can lead to pump cavitation—which damages equipment and lowers efficiency. It appears that even seemingly minor things can cause significant problems in complex systems.
9. The Reynolds number—a dimensionless quantity used to determine flow patterns—can tell engineers whether the flow is smooth (laminar) or chaotic (turbulent), drastically altering pumping needs. This insight into flow behavior allows for more accurate pump selection and improved energy-saving strategies. It's a fascinating example of how applying the right physics principles to engineering design can have practical benefits.
10. Flow rates aren't fixed; they change with demand and system conditions, so dynamic modeling methods are needed to predict behavior under different circumstances. This nuanced approach significantly strengthens the robustness and reliability of infrastructure designs. We need to design systems that can adjust to the ever-changing demands placed on them.
Understanding Pipe Volume Calculations A Step-by-Step Guide for Construction Professionals - Common Challenges in Construction Site Pipe Measurements
Accurately measuring pipes on construction sites can be surprisingly difficult and often leads to challenges that can impact project success. One common hurdle is simply gaining access to all parts of a pipe within a complex construction environment. This can lead to measurement errors that flow into calculations down the line. Additionally, pipes rarely exist in perfectly straight lines. Curves and intersections require more complex calculations than straightforward cylindrical formulas, which can be problematic if not considered carefully. Another source of potential errors stems from the manufacturing process itself, where slight variations in wall thickness and pipe diameter are common, making precise volume estimations challenging. These variations, even small ones, can significantly impact flow calculations. Because of this, construction professionals must be acutely aware of these measurement complexities to avoid errors that could lead to material waste, incorrect system sizing, and ultimately, more expensive projects.
1. Environmental conditions can introduce challenges to precise pipe measurements. For instance, temperature swings can cause expansion or contraction in pipe materials, potentially leading to inaccurate diameter readings. These discrepancies can then propagate errors in volume calculations and system designs, highlighting the need for careful consideration of environmental factors during measurement.
2. The chosen method of pipe installation can affect measurement accuracy. Trenchless techniques or traditional excavation methods can introduce challenges due to soil movement or equipment limitations. These complexities emphasize the importance of meticulous planning and flexible measurement strategies to ensure accurate results regardless of installation method.
3. Even the condition of the measuring instruments themselves can contribute to errors. Worn-out calipers or improperly calibrated measuring devices can introduce inaccuracies in the order of fractions of a millimeter, significantly affecting the integrity of subsequent volume calculations. This highlights the importance of instrument maintenance and calibration for reliable measurement outcomes.
4. Internal coatings or linings within pipes can impede accurate diameter measurements, as they can obscure the true inner diameter. This issue becomes particularly relevant in older systems where degradation might have occurred. Accurate estimation of flow rates and overall system performance relies on these inner diameter measurements, making this a critical aspect of measurement in the field.
5. It's crucial to remember that fluid flow behavior within pipes isn't solely governed by pipe diameter. Surface roughness, pipe material, and even the nature of flow (laminar or turbulent) significantly affect flow characteristics. Precise measurements become even more critical when accounting for these intricate fluid dynamic principles.
6. In systems with interconnected pipe sections, small variations in diameter along the network can accumulate and create unintended pressure drops. Engineers often focus on individual pipe segments rather than considering the collective impact of these variations throughout the system. This can lead to inefficiencies that become difficult to pinpoint during later troubleshooting phases.
7. Measuring pipes with non-standard shapes or fittings presents particular challenges. These geometries often require specialized measurement approaches that don't readily translate to conventional volume calculations. This underscores the need for adaptability and ingenuity in measurement strategies.
8. The connection points or joints between pipes are often overlooked when assessing friction losses. Industry standards often treat these joints as negligible, which might not always be valid. The impact of friction losses at junctions on both volume and flow rate calculations highlights the need for a more thorough approach to consider these interfaces.
9. Variations in pipe manufacturing can lead to discrepancies between the nominal and actual pipe dimensions. While design specifications might aim for uniformity, tolerances in fabrication mean the actual measurements can differ by several millimeters. This variability can impact fluid transport efficiency and system performance.
10. Finally, there are inherent limitations in the use of solely visible inspection methods for determining pipe diameter. Visual inspections can sometimes fail to detect underlying deformities or obstructions within the pipe. These hidden features can significantly decrease the effective volume and flow rates, which underscores the need for supplementary measurement and inspection techniques to fully characterize the condition of pipes within a system.
More Posts from mm-ais.com: