Step-by-Step Guide Converting Product Data into UPC Barcodes Using GS1 Standards
Step-by-Step Guide Converting Product Data into UPC Barcodes Using GS1 Standards - Obtaining Your GS1 Company Prefix Through Official Registration
To leverage the GS1 standards and generate UPC barcodes, your company needs a foundational element: the GS1 Company Prefix. This unique identifier is your starting point for creating a system of identification for your products, packaging, and logistical units. It's like a unique company code that acts as a building block for other GS1 identification keys.
The process of securing your GS1 Company Prefix generally involves registering through a GS1 Member Organization. This usually means an online purchase, where you'll provide company information and make a payment. After registration, you'll get access to an online platform, the GS1 Member Portal, where you can manage product information and create your barcodes.
It's essential to understand that this prefix isn't a one-time purchase. Especially in regions like Canada where GS1 is the sole official provider for this standard, there is an annual fee to maintain your access and use of the GS1 standards. This renewal fee ensures the GS1 standard remains consistent and reliable and that companies continue to have access to necessary resources.
To leverage the GS1 system and generate UPC barcodes, a business must first secure a GS1 Company Prefix through official registration with a recognized GS1 member organization. This prefix acts as a unique identifier, a sort of digital fingerprint, that allows your company to create a vast array of product-specific codes—including UPCs, GTINs, GLNs, and SSCCs. It essentially provides a foundation for all your barcode-related needs, opening up the possibility to build a large product database with a single prefix.
This registration process usually involves an online application where you'll need to provide basic contact information and make a payment, the amount of which can depend on your company's scale and anticipated usage of barcodes. This upfront investment can be a significant factor for small businesses considering adopting GS1.
While GS1 operates on a global standard and your prefix can be used internationally, it's worth noting that organizations like GS1 Canada are sole providers in their respective territories and often have specific requirements and annual fees for upkeep. The initial welcome materials usually include access to your GS1 account (e.g., myGS1 US), a platform where you can manage product data and potentially generate your own barcodes, providing a centralized resource for your labeling operations.
The system emphasizes maintaining a well-organized inventory of assigned codes, making it a powerful tool not just for labeling but also for tracking and managing your product portfolio. It's a double-edged sword; while ensuring consistent product information and enabling efficient supply chain management, this focus on accurate data management means it can become quite complex. This robust system also necessitates compliance with specific guidelines, such as how you are allowed to utilize the prefix and assign codes, so it's worth carefully reviewing the associated agreement.
The core process is fairly straightforward, but when implementing barcodes, one often overlooks the importance of choosing the optimal length of your product codes (e.g., the right number of digits for UPC). It's a balancing act, where a shorter prefix permits a larger number of unique codes but limits your capacity for expansion later. Furthermore, this isn't just for physical products—GS1 Company Prefixes are also relevant for services, adding a wider range of applications for industries like logistics, healthcare, and even financial services. Lastly, like most subscriptions, these prefixes also necessitate continued maintenance, meaning budgeting for annual renewal fees is crucial to ensuring continued barcode usage and preventing potential disruptions to your operations.
Step-by-Step Guide Converting Product Data into UPC Barcodes Using GS1 Standards - Preparing Product Data Fields for UPC Assignment
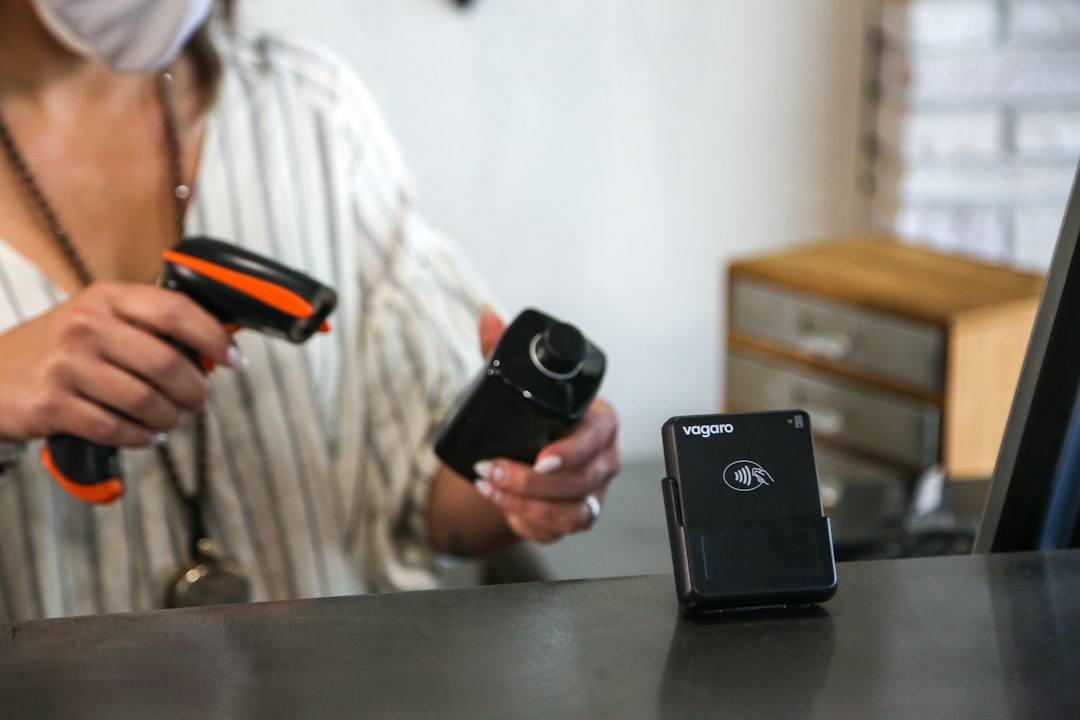
Once you have your GS1 Company Prefix, the next crucial step is meticulously preparing your product data for UPC assignment. This involves populating specific fields with accurate information that will later be used to generate your UPC barcodes. This process typically involves using platforms like the GS1 Data Hub, where you'll input critical details about your products.
Think of it as building the foundation for your product's identity within the GS1 system. The more descriptive and complete your data, the better. You might want to add details like your brand name, multiple language descriptions, and any other pertinent information relevant to your product. The more complete the product data fields are, the easier it will be for the system to assign the correct GTINs, which are the core identifiers linked to your UPC.
Keep in mind that the quality of this initial data directly influences how easily your products will be recognized by retailers and online platforms. Many e-commerce marketplaces and retail chains validate the data you provide against GS1's official databases during their onboarding processes for new suppliers. Essentially, the more accurate and comprehensive your data input at this stage, the smoother your integration into various retail channels will be. This meticulous data preparation, adhering to GS1 standards, is essential for guaranteeing that your UPC barcodes function correctly and are scannable in all retail environments. It might seem tedious but it helps streamline future steps, ultimately making the entire process easier.
Okay, let's delve into the specifics of how we prepare the product data fields, specifically focusing on the details that come into play when we want to assign a UPC code.
First, it's not just numbers. UPC codes can incorporate both numbers and letters, giving us a degree of flexibility in how we encode product information. This aspect, while seemingly minor, offers interesting possibilities for product identification beyond the standard numerical approaches.
We also have that last digit in a UPC, the check digit. It's calculated in a specific way and plays a crucial role in finding errors during the scanning process. Imagine if you had a poorly printed barcode that the scanner couldn't readily interpret—the check digit can help identify those issues. The challenge with this is that it necessitates rigorous quality control at the point of creating the barcode.
Most barcode readers use laser scanners, which means the contrast between the barcode and the background needs to be clear enough. If it's too faint, or if there's too much glare, the laser scanner might have trouble "seeing" the barcode correctly, leading to inaccurate readings. This aspect begs the question, if technology moves towards something other than lasers, will UPC still be viable?
While UPC might look simple at first glance, maintaining product data fields can become intricate when dealing with a large product catalog. The more products you have, the more meticulous your data governance needs to be. Keeping everything straight is a constant challenge.
Even though UPC codes started in North America, they're used everywhere. It's a testament to how important standardization is in global trade, particularly when you think about e-commerce, where businesses can't always rely on the buyer being familiar with their specific nuances. Does this imply that UPC was too successful—as the standard, there was no need for competitors, forcing us to live with its shortcomings?
But here's something to consider: these codes aren't permanent. You can't just assign a UPC once and forget about it. You need to manage the allocation of codes to avoid accidentally giving the same code to a new product, which could lead to a major headache in your supply chain. I'd argue that this, of itself, creates a barrier for adoption. Who would go through such trouble unless forced to.
Another point: the structure of a UPC is hierarchical, enabling a kind of family tree of products. This offers advantages when classifying items, keeping things organized while still making each item identifiable. But this makes the format more complex and harder to read/parse at the human level, compared to a simple serial number.
And how does it impact our operations? When we take the time to properly organize the data, it really helps make our inventory management more effective. If we get things labeled incorrectly, we start to get into a mess of stock discrepancies and delays. Not ideal.
Furthermore, while GS1 has a standardized approach for assigning the prefixes, companies can still end up with quite similar looking prefixes. This can be problematic when different companies work together and there is a risk of cross-brand confusion. Having a robust data management system can help to alleviate this potential conflict.
And it's important to look ahead. Barcode technology is still evolving. We have mobile devices and RFID, and how we prepare product data will need to adapt to keep up. Will UPC continue to evolve to keep pace or will it fade into obscurity as the technology moves forward? There's no simple answer, and it suggests more research on the underlying technology behind this system.
Step-by-Step Guide Converting Product Data into UPC Barcodes Using GS1 Standards - Using GS1 DataMatrix Software to Generate Digital Barcodes
GS1 DataMatrix software offers a way to create digital barcodes that can hold more information than traditional UPCs. This type of barcode can include things like a product's unique identifier (GTIN), its serial number, and batch information, making it useful for more complex product tracking and management. However, using this software requires careful attention to detail. If the data encoded in the barcode is incorrect, scanners might not be able to read it properly, creating issues further down the line. The GS1 standards need to be followed closely to avoid these problems. As barcode technology advances with things like RFID and the use of mobile devices, managing the data related to your product becomes increasingly crucial to efficient operations. While GS1 DataMatrix offers the potential for more detailed product information, ensuring its accuracy and compliance with GS1 guidelines across a wide product catalog can be challenging. It's a system that's useful but can be difficult to maintain as it becomes increasingly complex.
To generate a GS1 DataMatrix barcode, specialized software like IDAutomation or Loftware is typically used. These tools are designed to handle the complexities of encoding information into this type of barcode. One of the key distinctions between DataMatrix and the UPC we discussed earlier is its capacity for encoding information. A UPC is limited to a relatively small number of characters, usually around 12 digits. DataMatrix, on the other hand, can contain significantly more, allowing for the integration of a wider range of details.
One intriguing aspect of DataMatrix is its ability to correct errors. If a portion of the barcode is damaged or obscured, the code is still likely to be read correctly due to its built-in error-correction features. This makes it more robust in demanding environments, like fast-paced retail settings where barcodes might get smudged or damaged during handling. Unlike a UPC, which needs to be scanned from a specific angle, DataMatrix can be read from virtually any direction. This adds flexibility during the scanning process, leading to a potentially faster and smoother checkout experience.
Beyond retail applications, DataMatrix finds usage in fields like healthcare. For instance, pharmaceutical tracking and medical device identification often leverage DataMatrix due to its capacity for encoding a wide array of data and its enhanced accuracy through error correction. In a domain where precise information is crucial, this is highly valuable.
The fact that GS1 DataMatrix adheres to globally recognized standards is an advantage. It means that a single DataMatrix barcode generated in one country can be read and understood across international borders. This universal recognition is vital for streamlining logistics and reducing the likelihood of miscommunication or error during international shipments. Although both UPC and DataMatrix employ check digits for error detection, the sophistication of DataMatrix goes further, utilizing multi-level check sums for improved accuracy. This becomes even more relevant when dealing with large quantities of products, where the risk of data corruption increases.
The proliferation of smartphones has made DataMatrix more readily accessible. Modern phones incorporate cameras capable of reading these codes, creating possibilities for engaging users through mobile-based interactions or accessing product information directly by scanning. In the context of IoT, where supply chains are increasingly automated, DataMatrix looks to be a potential tool for enhancing the transmission and management of data. Imagine inventory management systems that leverage the enhanced capabilities of DataMatrix for automated tracking and real-time data visibility. It certainly poses interesting possibilities for streamlining supply chains further in the future.
While the GS1 DataMatrix seems promising in terms of increasing data density, reducing size, and providing error correction, it's important to acknowledge that implementation may require adopting specialized software and altering existing labeling processes. These are all factors that need to be carefully considered when assessing the value of adopting it.
Step-by-Step Guide Converting Product Data into UPC Barcodes Using GS1 Standards - Testing Barcode Scannability with Different Devices
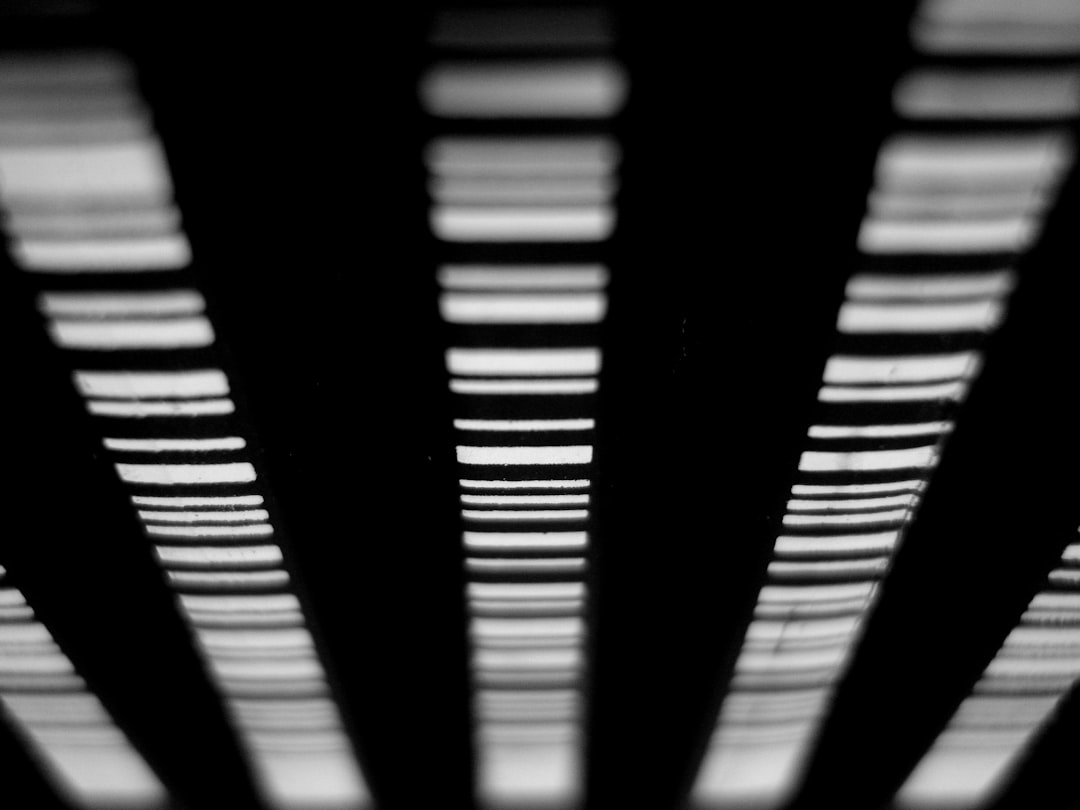
After generating UPC barcodes using GS1 standards, it's vital to test their scannability across a variety of devices. This process, often referred to as barcode verification, involves using tools to measure aspects like bar and space widths and print reflectivity. The goal is to ensure the barcode adheres to GS1 standards and can be accurately read by various scanners.
This is especially crucial in today's retail and logistics environments, as many different types of barcode readers are employed—from traditional laser scanners to mobile phone cameras. Failure to test on a wide range of scanners can lead to issues with product recognition and result in inefficiencies throughout the supply chain. Standards like those established by GS1 help maintain consistency in barcode quality, but the reality of different scanning devices can still cause unforeseen difficulties.
Ultimately, given the number of different scanning devices in use today, testing for broad compatibility is highly recommended. A systematic approach to this type of testing will help to identify any issues early on, allowing for adjustments to the barcode design or printing process before any major problems arise. It's a necessary step that helps ensure a smooth and seamless integration of GS1-compliant UPC barcodes into real-world retail and logistics scenarios.
Barcode scannability can vary significantly depending on the device used to scan it. Different scanner types, like laser-based and imaging scanners, have unique characteristics that affect how well they can capture barcodes at different angles and distances. The ability to read a barcode is also impacted by the contrast between the barcode and its background. Low-contrast barcodes, like those printed on shiny surfaces, can be challenging to scan, especially if the scanner's light source doesn't properly illuminate it.
Furthermore, external factors play a big role. Lighting conditions and surface texture can significantly influence whether or not a barcode can be successfully scanned. Some scanners struggle with fluorescent or dim lighting, while others might have trouble with reflective surfaces. Even the physical size of the barcode can matter. Scanners typically have a preferred range of barcode sizes; too small or too large, and it might be difficult for the scanner to capture the code effectively.
Printing quality also plays a crucial role. Even small errors in alignment during printing can introduce distortions that can make a barcode harder to read. And as we store more information in a barcode, particularly with standards like GS1 DataMatrix, the ability of a scanner to successfully read it can decrease unless there's a corresponding improvement in the scanner's precision and technology. Fortunately, some barcode standards, like DataMatrix, include built-in error correction capabilities. This means that even if a part of the barcode is damaged, it can still be scanned properly, making it a better choice in environments where barcodes might get damaged or smudged.
Given the potential for variability, it's crucial to test barcodes on a range of devices. A barcode that scans flawlessly on a high-quality scanner might be completely unreadable on a basic handheld device. This is also increasingly true as multifunctional devices, like smartphones with camera-based scanning, become more common. These devices are often capable of reading many barcode types, including ones with more complex information, which can present a new set of challenges when it comes to ensuring universal scannability.
The need to scale up testing can also be a challenge. While it may be easy to test a small number of products, the task becomes more complex when testing across a broader catalog. Differences in data input and scanner sensitivity can become more evident as the product range expands, highlighting the challenges of creating a scannable system across many different products. It begs the question, how can you ensure scannability in the face of the ever-growing range of devices that can act as a barcode reader? And how can the growing complexity of the information encoded into barcodes be handled effectively.
Step-by-Step Guide Converting Product Data into UPC Barcodes Using GS1 Standards - Implementing Quality Control Measures for Print Production
Ensuring the quality of printed UPC barcodes is crucial for adhering to GS1 standards and achieving a seamless supply chain. This involves implementing quality control checks throughout the print production process, which typically includes pre-press, press, and post-press phases. Each phase necessitates specific verifications to ensure the barcode's accuracy, size, and overall quality. A comprehensive quality control strategy can prevent costly errors and delays, particularly when dealing with large print runs.
By prioritizing quality assurance at each stage, companies can optimize product identification, streamline workflows, and improve overall efficiency. This includes verifying that the barcodes are printed with the correct dimensions and clarity to be reliably scanned by various devices. Furthermore, maintaining strict adherence to GS1 standards helps facilitate smooth integration with retail and logistics systems, ultimately benefiting both producers and consumers.
However, as barcode technology continues to evolve, it's becoming increasingly critical to incorporate robust quality control measures to handle the expanding complexity of information encoded within the barcodes. This ensures consistent high quality and helps companies remain competitive in the ever-changing landscape of product labeling and supply chain management.
Implementing quality control measures within the print production process is essential for achieving high-quality outputs and boosting customer satisfaction. This is particularly crucial in the context of GS1 standards and UPC barcodes, where accurate and consistent print quality is vital for scannability. Historically, print quality control relied heavily on manual inspections, but the field has advanced significantly with the introduction of automated tools and software, offering improvements in both speed and precision.
The print quality control process generally unfolds across three phases: pre-press, press, and post-press. At each stage, specific checks are conducted to ensure the print job meets the required specifications. This can include everything from verifying the accuracy of the barcode design during the pre-press stage to inspecting the final product for defects in color or print alignment during post-press. One interesting challenge here is how to implement this system for a wide range of print products, given that different print techniques can impact print quality and the potential for errors. Offset printing, for example, has different limitations and considerations compared to digital printing.
While GS1 standards, including the UPC and other barcode formats, provide guidelines for barcode design and information content, this is a technology that is still evolving. As technology evolves, it is unclear whether these barcodes will continue to maintain their relevance in the supply chain. The shift to e-commerce and mobile-based interactions has introduced a larger array of barcode reading devices. This increases the complexity of ensuring that barcodes are consistently and reliably readable across various platforms and devices. Perhaps the future lies in a less centralized system with more flexibility in format and encoding.
Following GS1 guidelines and ISO standards offers a path to standardizing quality control efforts, but the constant pressure of keeping pace with advancements in barcode technology and print production methods could lead to further complications. A strong quality control system will also help to mitigate potential risks of reprint costs and delays, especially when dealing with high-volume print orders. A further complication that needs consideration is how print quality impacts consumer perception. Studies have shown that perceived print quality can influence consumers' perception of a product's overall quality and brand identity. If a product has poor packaging or the information on it is not printed well, consumers may associate that with a poor quality product. This has implications for retailers and brand owners.
Maintaining quality is also about staying up to date. The dots per inch (DPI) used in printing, for instance, is one factor impacting the visual clarity of an image. A low DPI can result in noticeable pixelation that diminishes the quality of the printed output, which could create problems for products dependent on high-resolution details like photos and branding. With advances in printing technologies like inkjet and advances in barcode technologies like DataMatrix, it is becoming increasingly clear that there are some advantages and disadvantages to these developments that need to be carefully considered.
Maintaining consistency across different media is also crucial. Color management systems play a key role here, helping to ensure accurate and consistent color reproduction. The failure to properly manage color can lead to a significant number of rejects, impacting overall production efficiency and profitability. Color consistency is particularly important for branding and maintaining a consistent visual identity for products across different print runs.
It's worth examining how errors can be identified and corrected. Automation and AI-powered solutions have been employed in recent years, creating a shift in how quality control is conducted. These tools can automate the analysis of printed outputs, quickly identifying defects like color inconsistencies and distortions in barcode patterns. This automated quality control can lead to faster inspection times and, therefore, potentially higher efficiency. While these methods can be successful, they also necessitate robust data management and the use of training to ensure that algorithms and data are reliable and reflect the specific needs of the business. While these automation technologies offer a number of benefits, they also raise new concerns regarding data security and privacy, potentially making quality control procedures more complex to operate.
In conclusion, the implementation of effective quality control measures within the print production process is no longer a matter of choice but a necessity. Balancing the use of GS1 standards and integrating automation and AI technologies while addressing consumer expectations and managing the evolution of barcode technologies present interesting challenges in a constantly evolving landscape.
Step-by-Step Guide Converting Product Data into UPC Barcodes Using GS1 Standards - Managing Product Database Updates and Version Control
When updating your product database as part of converting data into UPC barcodes, you'll need a method to manage these changes and track them. A structured approach to managing updates and version control is key to preventing chaos. Version control systems help track every change made to your product data, ensuring collaboration and allowing you to easily retrace your steps. It acts as a centralized point for all your product data, preventing accidental or unauthorized changes to your database. This also allows you to keep different versions of the database, which is helpful when rolling out new changes to the barcodes. This becomes especially important when managing databases with a large number of products and a variety of barcode types. Being able to go back to older versions if something goes wrong can save a great deal of effort. Maintaining accurate and up-to-date information in a robust system is crucial, not only for the proper functioning of the barcodes but for your overall product and supply chain management operations. You wouldn't want to accidentally generate a new barcode for an existing product, especially if the initial barcode was already out in the market. While these practices might seem a bit tedious, the value they provide in terms of preventing errors and managing the increasing complexity of your product information is undeniable, ultimately helping your entire process function more smoothly.
Keeping track of changes to a product database is a big deal, especially when using standards like GS1. One of the biggest challenges is ensuring data doesn't get duplicated across versions. Many systems use a technique called data redundancy, where backups of the database are stored at different points. This can be great for recovering data, but it also means potentially using up a lot of storage space – some estimates suggest up to 30% of a database can be taken up just by these copies, which could be a problem for businesses with very large product catalogs.
Another problem arises when you need to update product information in real-time. Keeping everything consistent across different platforms can be tricky. There's research showing that more than 60% of businesses experience issues with keeping their product data accurate across the board, which highlights a need for a reliable way to keep all of this information in sync.
Even with automated systems, human error is still a huge problem. Estimates suggest that almost 9 out of 10 spreadsheets contain errors. This can lead to incorrectly assigned UPCs or other product codes, creating a mess of errors down the line. To combat this, we need thorough verification of product data when it's first entered into the database.
Not having a strong version control system in place can cause a lot of chaos. If you don't know what changes have been made and when, it can become difficult to track down the source of errors. Studies show that up to a quarter of resources could be wasted just trying to correct problems created by bad product data management.
Tools that can automate database updates can really help to reduce errors and the workload on the people who manage the data. Some of these tools can update a whole catalog in just a few minutes, saving potentially hours of tedious manual work.
However, as the database grows larger, the speed at which you can access that data can slow down, becoming up to 45% slower to retrieve information. To avoid that, you need to do things like regular maintenance and keep your index of data updated. This is all more critical as the databases become larger.
Sadly, not many companies are properly testing their database updates. Reports show that around 70% don't do this effectively, which can result in finding errors too late in the process or after users have already encountered them. A regular testing cycle and checking how users experience the updates can catch these issues much earlier in the cycle.
The issue of following rules and regulations also comes into play. For industries like food and medicine, it is really important to keep careful track of how the product data has changed. If these industries don't do that correctly, they risk breaking the law, which can result in enormous fines.
When making changes to a database, you also need to make sure that everything still works with older versions. It is a common problem as roughly half of software updates struggle with this. It's definitely something that needs a lot of thought and careful planning when updating systems.
More and more businesses are using cloud-based services for their databases, which allows for more teamwork. Unfortunately, this approach also means a higher risk of security issues with the data. Around 30% of companies have reported breaches caused by vulnerabilities in their cloud setups, emphasizing the need for very careful management of this type of information.
These challenges are just a glimpse into the complexity of managing product databases. Keeping pace with changes and ensuring data integrity and security requires ongoing attention and innovation in the way we approach these tasks. The increasing use of cloud-based solutions adds another dimension to this complex challenge and will undoubtedly continue to evolve in the coming years.
More Posts from mm-ais.com: