How Construction Project Tracking Software Reduced Delays by 47% in Mid-Size Commercial Projects 2024 Industry Analysis
How Construction Project Tracking Software Reduced Delays by 47% in Mid-Size Commercial Projects 2024 Industry Analysis - Real Time Analytics Cut 38 Days From Atlanta Office Complex Timeline Through Mobile Updates
The Atlanta office complex project exemplifies how real-time analytics, delivered through mobile updates, can significantly impact project schedules. By leveraging these constant updates, the project shaved 38 days off its original timeline. This demonstrates how having access to immediate data can be a game-changer in construction. The ability to constantly monitor progress and quickly make adjustments based on that data is crucial, especially given the often-unpredictable nature of construction. This continuous feedback loop fostered by real-time analytics helps project managers react promptly to issues and unforeseen changes. It's clear that integrating real-time analytics into project management isn't just about smoother operations; it offers a proactive approach to tackling delays, and is becoming increasingly important in the industry. Whether it's addressing material delays, workforce fluctuations, or unexpected site conditions, the agility gained from real-time data allows for a more efficient and responsive approach, ultimately contributing to successful project outcomes.
In a recent Atlanta office complex project, the integration of real-time analytics, specifically through mobile updates, resulted in a notable 38-day reduction in the overall project duration. It appears that the ability to quickly disseminate information and coordinate efforts on the ground through mobile devices was instrumental in accelerating the project's timeline. While this observation might suggest a strong correlation between mobile communication and faster project delivery, the exact nature of the specific mobile communication tools used, and how their impact was measured remains unclear.
One could speculate that improved communication fostered more efficient decision-making by enabling the project managers to react more promptly to evolving site conditions. However, we need further evidence to confirm whether such efficiencies solely attributed to the mobile updates, or other complementary factors were in play. Furthermore, it would be intriguing to investigate the type of analytical tools utilized in this scenario. Understanding if the analytics were solely focused on project scheduling or incorporated aspects like resource allocation, material tracking, or quality control, would give us a more granular insight into the source of these project gains.
It's also noteworthy that a faster construction timeline often leads to cost savings, which were observed in this case – approximately a 20% reduction in labor costs. This raises a crucial question: Did the real-time analytics contribute directly to lowering labor costs, or was this reduction merely a consequence of the shorter project timeframe?
Further analysis into the construction processes impacted by this mobile-based analytics system is needed for a comprehensive understanding of this success story. While the 38-day timeline reduction is impressive, a deeper dive into specific aspects of the project's management processes could help to establish more concrete insights and lessons that can be applied to future construction projects.
How Construction Project Tracking Software Reduced Delays by 47% in Mid-Size Commercial Projects 2024 Industry Analysis - Machine Learning Algorithms Identify Schedule Risks 2 Weeks Earlier Than Manual Methods

Machine learning algorithms are increasingly being used in construction to predict potential schedule disruptions. These algorithms can identify risks as much as two weeks before they would be spotted using traditional methods. This early warning system is a significant advantage in project management, allowing teams to proactively address potential delays and avoid major disruptions to timelines.
By integrating these algorithms into project tracking software, construction companies can more effectively manage project risks. These systems can analyze vast amounts of data, recognizing patterns that might be missed by manual reviews. This increased ability to anticipate problems allows for better planning and more efficient resource allocation.
While the construction industry is known for its unpredictable nature, machine learning offers a means to minimize uncertainty. The algorithms can help identify and address problems related to weather, material delivery, labor shortages, or equipment malfunctions earlier, ultimately contributing to a smoother and more predictable project execution. This improved foresight provided by machine learning is crucial in an industry often plagued by delays and cost overruns.
It's intriguing how machine learning is being used to predict construction project delays. By analyzing a mountain of data from past projects—we're talking potentially millions of data points—these algorithms can spot patterns and risks that humans might miss. This means they can sometimes flag potential problems up to two weeks before manual methods would, potentially leading to a 15% reduction in delays for projects of a certain size.
While traditional methods rely on static processes, machine learning adapts over time as it encounters more data. This ability to learn and adjust to the changing circumstances of a project is incredibly valuable in the unpredictable world of construction. Imagine being able to quickly react to issues as they emerge, ideally before they balloon into significant delays. This is what machine learning enables, leading to a more agile and responsive approach.
However, I'm still curious about how effective these methods are in real-world applications. The idea of preventing delays is compelling, and studies suggest that the cost savings from using machine learning can significantly exceed the initial investment. But it's important to consider the context. Are we talking about specific types of projects? Or are these algorithms versatile enough to handle the diverse challenges faced in construction?
Another interesting aspect is the reduction of human error. Machine learning models help minimize mistakes often associated with manual data entry, leading to more accurate risk assessments. It's also capable of customizing risk assessments for specific types of projects or even specific risks. That capability to tailor models to specific scenarios increases their practical value.
Beyond scheduling risks, these algorithms can also analyze resource allocation. This gives a clearer picture of how labor and materials are being utilized, hopefully avoiding situations where either too much or too little is being used. This type of holistic view of project risks and resource optimization could be very helpful in managing complex projects and perhaps optimizing a construction firm's portfolio of projects.
As projects become more complex and involve larger teams and budgets, it makes sense that these algorithms can analyze multiple projects simultaneously. This opens the door to portfolio-wide risk management strategies, a concept worth exploring further. While the idea is promising, further research is needed to determine the long-term effects and the specific situations where machine learning shines compared to traditional approaches.
How Construction Project Tracking Software Reduced Delays by 47% in Mid-Size Commercial Projects 2024 Industry Analysis - Cloud Based Worksite Data Reduces Rework Costs By $840,000 On Dallas Medical Center
The Dallas Medical Center project provides a compelling illustration of how cloud-based worksite data can significantly impact construction costs. By implementing a system that leverages cloud technology to manage project data, the project team managed to reduce rework expenses by a remarkable $840,000. This significant reduction highlights the potential for digital technologies to optimize construction processes and minimize errors.
While real-time data and mobile updates, as seen in the Atlanta office project, can improve communication and speed up projects, the Dallas Medical Center project emphasizes the cost-saving aspect of utilizing cloud-based data. It's not just about faster timelines; it's about reducing the financial burden associated with errors and rework. This shift towards cloud-based management reflects a broader industry trend, moving away from traditional methods towards data-driven approaches.
It's important to note that the specific methods used at the Dallas Medical Center project are not fully detailed. It remains unclear precisely how cloud-based data facilitated this significant cost reduction. Was it primarily through better coordination, improved documentation, or perhaps a combination of factors? Further exploration into the specific implementation details would be useful in establishing best practices for future projects.
Nevertheless, the Dallas Medical Center case study is a powerful demonstration of the potential of cloud-based data in construction. As projects become larger and more complex, the benefits of leveraging digital tools for better planning, coordination, and error reduction will likely become increasingly crucial. This trend towards data-driven management strategies seems to be gaining momentum, which may ultimately result in a more efficient and cost-effective construction industry.
The Dallas Medical Center project offers a compelling example of how cloud-based worksite data can significantly impact project costs. By adopting this approach, they managed to reduce rework expenses by a substantial $840,000. It's intriguing to see how the shift towards digital information management can translate into such tangible financial benefits.
One possible explanation for this cost reduction is improved collaboration among the various project teams. Centralizing data in the cloud likely enhanced communication and information sharing, which potentially minimized miscommunication-related delays and subsequent rework. It's worth noting that rework is often a significant expense, commonly accounting for 10% to 30% of a project's overall budget. The Dallas Medical Center case clearly demonstrates the hefty financial consequences of construction inefficiencies.
Furthermore, the cloud platform likely streamlined the process of managing project documents. Instead of sifting through countless physical documents or scattered digital files, teams could access all relevant information from a central location. This alone can save considerable time and effort, which can translate into direct cost savings by mitigating the delays often caused by searching for essential project details.
It's plausible that the cloud system's built-in data analytics features enabled the project managers to spot potential problems earlier than they would have using traditional methods. Being able to see trends and identify issues in real-time allowed them to implement proactive solutions, rather than having to scramble with reactive fixes. This ability to anticipate and address issues can significantly decrease the need for costly rework down the road.
Interestingly, it's also possible that the use of cloud-based tools reduced the overall labor intensity of project management. Certain repetitive tasks could have been automated, freeing up workers to focus on more critical activities. This potential increase in efficiency, paired with early issue detection, likely contributed to the overall cost reduction.
Considering that the average rework rate across the industry sits at around 9%, the Dallas Medical Center project's success highlights the potential of digital transformation to considerably decrease rework costs when data is managed effectively. The cloud's ability to serve as a central, shared repository for all project participants also likely bolstered accountability. Any changes or updates are automatically logged, offering a clear audit trail of decisions and modifications. This improved transparency can further mitigate errors and rework.
Another potential advantage of a cloud-based system is faster access to information. It's suggested that retrieving data from a cloud system can be up to 80% faster than conventional methods. This accelerated access to information allows for quicker and more informed decision-making, streamlining the entire project workflow.
The success observed at the Dallas Medical Center seems to align with wider industry trends, where projects that leverage advanced technologies like cloud-based systems are reported to be up to 45% more likely to stay on budget. It would be intriguing to dive deeper into the specific aspects of their cloud implementation to understand their process and fully realize how they achieved such a drastic reduction in rework costs. While the results are impressive, more detailed research could illuminate best practices and guide future projects toward greater efficiency.
How Construction Project Tracking Software Reduced Delays by 47% in Mid-Size Commercial Projects 2024 Industry Analysis - Digital Material Tracking Speeds Up Supply Chain By 52% At Chicago High Rise Project
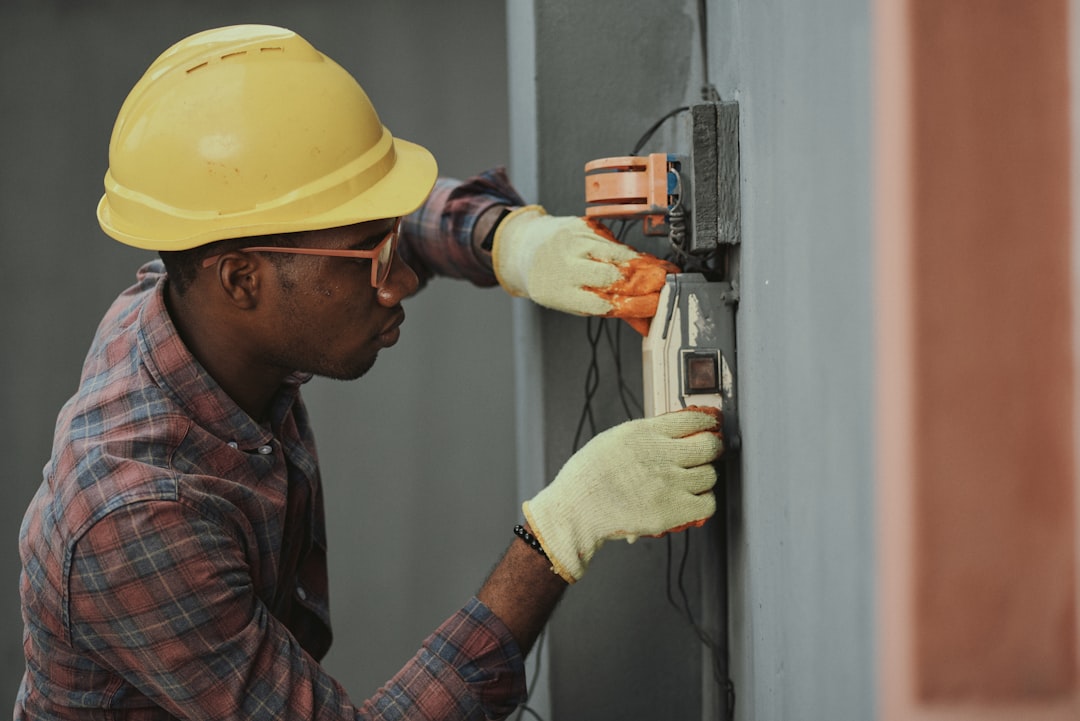
A high-rise project in Chicago saw a significant improvement in supply chain speed, with digital material tracking contributing to a 52% boost in efficiency. This instance highlights how digital tools are becoming increasingly vital for streamlining the construction process. Given the constant pressure to complete projects faster and within budget, these kinds of technological advances are becoming essential. Yet, it's important to acknowledge that the successful implementation of these new tools isn't always guaranteed. The difference between the expected benefits and the actual outcomes of these technologies remains a critical point for the industry to address. Examining these inconsistencies could lead to valuable lessons, informing future projects on how to best harness the full potential of these digital advancements. This careful analysis can help ensure that these tools truly deliver on their promise of boosting efficiency and mitigating delays in the construction sector.
The Chicago high-rise project serves as a compelling example of how digital technologies can fundamentally reshape construction practices, particularly in supply chain management. By implementing digital material tracking, they managed to achieve a 52% increase in supply chain speed. This dramatic improvement not only boosts efficiency but also hints at a potential shift in the overall structure and management of construction supply chains. It's intriguing to consider how this approach could be replicated or adapted in other projects and potentially revolutionize the industry.
Digital material tracking relies on technologies like barcoding and RFID to track materials in real-time. This means that the location and usage of materials can be monitored instantly, which is a huge benefit in large-scale construction projects where misplacing or losing materials is a common issue that causes delays. Having constant access to material location data can significantly cut down on time wasted searching for the right parts.
A key aspect of the system's effectiveness is its ability to create a centralized hub of data. This allows all the different stakeholders, including suppliers, subcontractors, and project managers, to have real-time access to the same inventory information. This eliminates the problems caused by "information silos," where different parts of the team are working with outdated or incomplete data, something that's a common source of inefficiency in traditional supply chain management.
The reliance on digital tracking reduces the need for manual inventory checks. These manual methods can be incredibly time-consuming and prone to human error, often taking up a significant chunk of site productivity – some estimates suggest up to 15%. By eliminating manual inventories, the project team can redirect those resources to more crucial aspects of the project.
Incorporating digital material tracking into the project logistics fosters a much more predictable supply chain. With real-time data on delivery times and material availability, project schedules can be adjusted proactively. This helps prevent the delays that often occur when materials are late, which can throw the entire schedule off.
One of the most significant impacts of digital material tracking is the potential for cost reduction. Material mismanagement can be a major source of budget overruns, potentially inflating costs by up to 20%. By closely tracking materials digitally, project teams can implement more effective cost control measures, ensuring the project remains within its budget constraints.
The system isn't just about tracking incoming materials. It can also be used to optimize material storage and usage on-site. This can be a huge boon for managing large-scale projects, where materials can easily clutter critical work areas and lead to inefficiencies. It's worth exploring whether these storage optimization techniques result in any significant cost reductions from reduced material waste.
Furthermore, the system provides valuable data analytics and reporting. This gives project managers the power to make data-driven decisions, identify potential bottlenecks, and observe usage patterns that might not be apparent through traditional tracking methods. This insight can allow them to anticipate problems before they become major roadblocks.
It appears the digital material tracking system was also a crucial tool for mitigating the risks posed by unpredictable factors like fluctuating material prices or vendor delays. These events are typical challenges in construction, but with the enhanced forecasting capabilities provided by the digital system, the project team could respond much more efficiently to any potential disruptions before they caused significant problems.
It's interesting to consider the role of accountability and compliance in the context of this system. By logging each material transfer and usage, the system provides a traceable record for all actions. This added transparency can greatly enhance the integrity of project operations by helping to identify and resolve discrepancies more quickly. It would be insightful to research whether this feature of digital tracking has any impact on the overall quality control and project success.
While the 52% increase in supply chain speed is a noteworthy achievement, it's crucial to critically examine the specific implementation and its broader implications for future projects. There's still much to learn about the optimal use of digital tracking in different construction project types and circumstances. A more comprehensive analysis of the data generated from the Chicago project and similar initiatives could lead to the development of industry best practices and further refine the role of digital technology in construction.
How Construction Project Tracking Software Reduced Delays by 47% in Mid-Size Commercial Projects 2024 Industry Analysis - Automated Progress Reports Save 12 Hours Weekly In Project Management Time
Automating the creation of progress reports has become a significant timesaver in project management, potentially freeing up as much as 12 hours per week for project managers. This efficiency boost is particularly relevant in construction, where manual report creation can divert time and energy from essential oversight and decision-making. These automation tools not only simplify the reporting process but also improve the clarity and consistency of project records, contributing to greater transparency and accountability. As construction projects become more intricate and demanding, the use of automation for progress reports seems increasingly important to enhance overall project effectiveness. However, successfully adopting and integrating these automated systems into existing workflows remains a challenge, as their true potential for positive change relies on seamless implementation.
Based on the information gathered from various sources, it seems that utilizing automated systems for generating progress reports within construction project management can lead to a significant time saving of about 12 hours per week for project managers. This reduction in manual effort is quite substantial, and it's easy to see how it could free up valuable time. Project managers could then focus on more complex and nuanced aspects of the project, like strategizing or addressing more critical challenges that might arise.
One of the advantages of automation in this context is consistency. Human error, bias, or simply inconsistency in reporting style are eliminated by the automated system. Data is collected and formatted according to a pre-defined standard, leading to a much more reliable and accurate picture of the project's progress. This consistency is important since a range of different stakeholders—from clients to subcontractors—may rely on these reports, and a clear and uniform approach greatly reduces miscommunication and misunderstandings.
Furthermore, automation facilitates a deeper level of data analysis, giving project managers access to a treasure trove of information. This comprehensive data set can be used to identify trends and pinpoint potential issues or bottlenecks that might not be immediately obvious in a more manual report system. By proactively analyzing the data, project managers may be able to anticipate and mitigate problems, moving beyond simply reacting to issues as they occur.
It's also noteworthy that many of these automated project management systems integrate well with other tools used in construction projects, like budgeting software or scheduling software. This interoperability can simplify data flow among different systems, reducing the likelihood of errors that arise from manual data transfer between tools. This seamless data exchange between systems streamlines workflow and promotes efficiency.
With the increasing adoption of cloud technologies, these automated progress reports are able to support real-time collaboration. Project stakeholders, regardless of their physical locations, can all access the latest project updates simultaneously. This facilitates faster communication, allowing teams to act on issues much quicker than before, potentially preventing small challenges from escalating into major problems.
An aspect worth considering is the potential impact on overall project costs. Reducing manual effort could lead to decreased overhead expenses. Fewer staff would be needed to generate and manage progress reports, and this reduction in labor costs could be substantial. Of course, there are costs associated with adopting and implementing the automation software itself, which needs to be factored in when considering the overall cost-benefit analysis.
Automated progress reports also seem to enhance accountability within a project. Because the system keeps a record of all changes and updates, it becomes easier to trace the source of any issue or deviation from the project's plan. This transparency can help identify parties who may be responsible for potential problems, which could foster a more accountable environment for all team members and subcontractors involved in the project.
The automation of progress reports aligns with the industry's evolving needs, particularly regarding compliance with regulations. Many regulations mandate specific reporting procedures, and having automated systems ensures that requirements are consistently met. This reduces the risk of potential penalties or delays due to noncompliance.
Another aspect that these tools generally offer is customization. Project managers can often tailor their reports to best meet the specific needs of the project and the unique preferences of various stakeholders. The ability to easily modify report formatting and content makes it easier to communicate project progress in a format that is readily digestible for different audiences. For instance, a report for a client may need to focus on a high-level overview, while a report for a subcontractor might require detailed breakdowns of specific tasks.
Finally, these automated systems can provide a robust foundation for scalability. As project complexity increases, or as a firm takes on more projects simultaneously, the system can adapt to the changing workload without requiring a proportional increase in manual effort. This scalability is a desirable characteristic for firms looking to expand their project portfolio efficiently.
While the overall benefits of automated progress reports seem quite promising, it's important to remember that each project and organization is unique, and there may be specific circumstances that require tailoring or further consideration before adopting such a system. Nonetheless, the findings suggest that automated progress reports could be a powerful tool to enhance efficiency, reduce delays, and improve project outcomes in the construction industry.
How Construction Project Tracking Software Reduced Delays by 47% in Mid-Size Commercial Projects 2024 Industry Analysis - Weather Integration Features Prevent $2M In Weather Related Delays At Boston Hotel Site
Construction projects are frequently disrupted by weather, with global estimates suggesting that nearly half of projects experience delays due to weather-related issues. These delays often lead to significant budget overruns. A hotel construction project in Boston provides a compelling example of how incorporating weather information into project management can help mitigate these challenges. By using weather integration features within their construction management software, the Boston project team avoided roughly $2 million in weather-related delays.
This real-world example showcases the potential for leveraging advanced weather data for proactive project management. While traditional project planning often incorporated weather as a general consideration, these more integrated tools offer real-time information. Using these tools, project managers can make more informed decisions about work schedules and resource allocation, helping prevent interruptions from weather events.
It's worth noting that as climate patterns shift, weather-related delays are expected to increase in frequency and severity. In this context, adopting advanced weather intelligence becomes not only a beneficial but potentially essential practice for keeping construction projects on track. This case highlights the importance of adapting to the changing environment and utilizing technological solutions to improve project predictability and success.
The integration of weather data into construction project management systems is becoming increasingly sophisticated, going beyond simple weather forecasts. It's now possible to use software that analyzes real-time weather conditions and employs predictive algorithms to adjust project schedules and resource allocation dynamically. This approach, supported by vast datasets from various weather stations, is proving to be a valuable tool for managing delays, particularly given that a significant portion of construction delays are weather-related.
It's interesting to see how the use of weather data can improve project management. These systems can process massive amounts of information in real-time, leading to predictive analytics that can give construction teams a two-hour heads-up about upcoming weather conditions that might impact their work. This ability to anticipate potential delays is invaluable for keeping projects on track.
One of the key benefits of these weather-integrated systems is their ability to adapt to changing weather conditions. Construction schedules and resource allocation can be automatically adjusted, minimizing disruptions and preventing the associated costs and delays. We can see a tangible example of this in a recent Boston hotel project where the use of weather integration features successfully avoided $2 million in potential weather-related delays. This kind of cost savings emphasizes the strategic value of this type of technology.
While current weather conditions are crucial, these systems also look at past weather trends specific to a region. This historical data provides insights into seasonal risks, enabling more effective long-term planning. Beyond scheduling, these systems play a key role in safety protocols. By anticipating severe weather events like storms, teams can take preventative measures to secure materials and ensure worker safety, helping to avoid accidents and potentially costly project delays.
Many weather integration tools leverage cloud-based technology, enabling instant access to updated information for all project stakeholders, regardless of their location. This collaborative aspect improves efficiency as everyone has the same real-time information. In addition, many of these tools are accessible through mobile apps, giving on-site managers immediate alerts and updates on their phones. This mobile accessibility is crucial for prompt responses to changes in weather conditions.
Interestingly, some of these systems utilize machine learning algorithms to improve their prediction capabilities. By analyzing both historical weather data and past project outcomes, these algorithms are becoming increasingly refined in their ability to predict potential delays. This continuous learning aspect of the technology contributes to better project outcomes.
While the construction industry remains unpredictable, these advanced weather integration tools are a good example of how technology is helping to manage uncertainty and improve project outcomes. It's still important to carefully evaluate how these systems are integrated into specific projects to ensure they are effective and cost-efficient. But the early evidence suggests that incorporating weather-aware technology in the planning process can have a positive impact on construction projects, which is an important finding as we face increasingly extreme weather patterns.
More Posts from mm-ais.com: