7 Lesser-Known Manufacturing Overhead Costs Driving Up Production Expenses in 2024
7 Lesser-Known Manufacturing Overhead Costs Driving Up Production Expenses in 2024 - Unplanned Equipment Downtime Costs Rise 22% Due to Supply Chain Delays
The situation with unscheduled equipment stoppages is getting worse. Costs associated with these events have jumped by 22%, largely due to ongoing issues within supply chains. US-based companies are seeing average hourly losses of around $103,000 when machinery unexpectedly goes offline, and the picture is even bleaker when looking at the global scale. It is hard to believe, given such heavy losses, that a notable portion of businesses still lean on reactive, fix-it-when-it-breaks maintenance tactics. This is only making matters worse. This whole mess leads to missed sales and hurts the bottom line, underscoring just how vital it is for firms to change their approach to maintenance and logistical planning. With unplanned downtime becoming an increasingly expensive headache, companies really need to consider whether they are making the right moves when it comes to equipment maintenance and upgrades.
Unexpected machine breakdowns are hammering businesses hard, especially with the current mess in the supply chain. Looking at the numbers, it's pretty grim. Back in 2021, the cost of just getting things from point A to point B jumped by 22% – and it's still climbing. This chaos is costing companies a mind-boggling $1.6 trillion in lost revenue. Even when a company tries to do the right thing and plans for downtime, they still get hit with hidden costs, like having to deal with a complete halt in operations or trying to salvage data. On the flip side, it appears that some are starting to wake up to this issue, as nearly half of those surveyed are planning to change their maintenance strategies or upgrade their equipment to mitigate downtime. A typical company in the US is losing about $103,000 every hour a machine is unexpectedly down, a little less than the global average of $125,000, but still a huge chunk of change. Shockingly, over two-thirds of these industrial companies are dealing with these surprise outages every single month. I find it hard to believe that over a fifth of them are just waiting for things to break before fixing them, despite the high costs involved. It's not just me saying this; industry analyses suggest this kind of downtime can cost a company upwards of $260,000 every hour. No wonder they say there's a need to change how maintenance is done or to just get newer equipment, but one has to wonder how many are just throwing money at the problem without a real plan.
7 Lesser-Known Manufacturing Overhead Costs Driving Up Production Expenses in 2024 - Digital Security Expenses Jump from Factory IoT Network Expansions
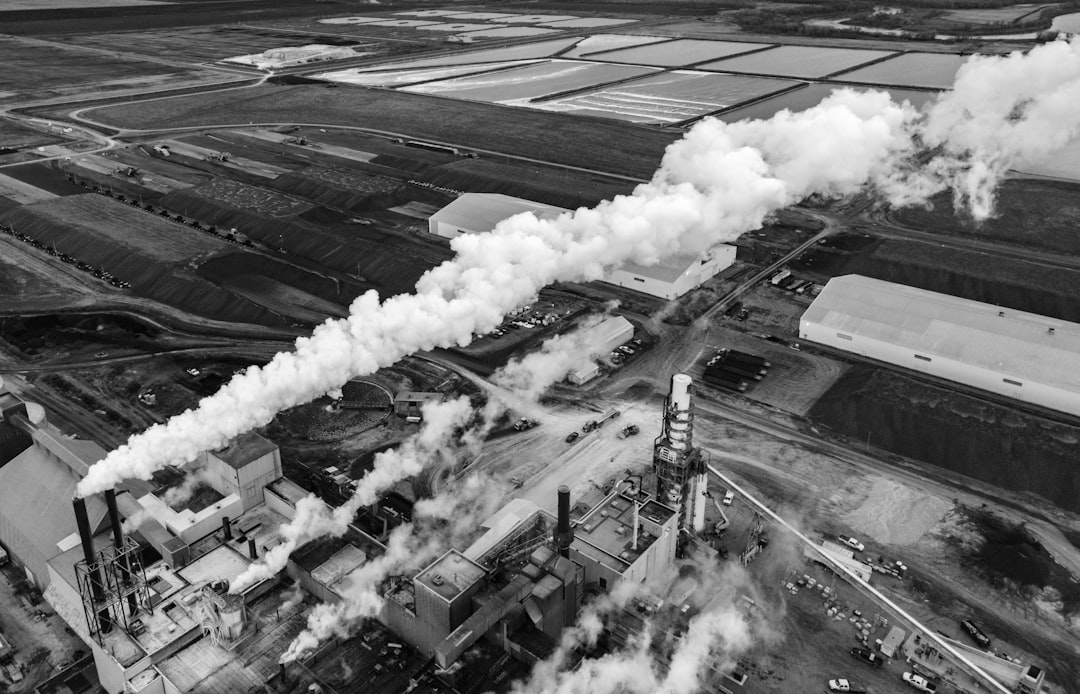
As manufacturers integrate more and more devices into their factory networks, the financial burden of maintaining digital security is growing. The sector is currently experiencing the highest share of cyberattacks compared to other industries globally. Shifting from legacy systems to modern Industrial Internet of Things technologies is not just a matter of keeping up with technological advancements, it involves hefty financial commitments to bolster cybersecurity infrastructure. Many are struggling not only with the adoption of Industry 4.0 technologies but also with securing the increasingly complex digital networks that come with them. There is a real risk that the cost of overlooking digital security today could be far greater than the investment required to secure it now. There are also arguments that security technologies such as blockchain are emerging as protective measures against data tampering and unauthorized network access. The bottom line is that amid ongoing digital expansion, strengthening cyber defenses is vital.
As manufacturers embrace the era of connected factories, with things like sensor networks enhancing how we measure and manage production parameters, they are also opening a Pandora's box of digital security headaches. It seems for every step forward in operational efficiency, there's a leap in the complexity and cost of keeping these systems safe from cyber threats. Recent figures suggest that digital security expenses are skyrocketing, up to 45% in some cases, thanks to these IoT network expansions. The more devices we connect, the more vulnerabilities we introduce, and it is not just about the tech; half of the manufacturing workforce hasn't been trained on cybersecurity, leaving a glaring gap that hackers can, and do, exploit. Data tampering in these networks is a real threat, and while blockchain technology is being touted as a strong protective measure, allowing only whitelisted devices to access operational networks, it is not a panacea. Around 70% of firms reported cyberattacks targeting their IoT devices last year. And, with each security breach potentially leading to millions in damages and days of downtime, it is no wonder that cyber insurance premiums are through the roof. The industry is clearly struggling with a fundamental shift, attempting to balance the need for increased labor productivity against the massive overhead of securing a smart factory. Some surveys suggest that only 30% of manufacturers have even bothered to conduct thorough risk assessments for their IoT networks, and despite the clear and present danger, 40% are prioritizing expansion over security. It begs the question, are we putting the cart before the horse, rushing into digital transformation without properly considering the defenses we need? There is an urgency now, driven by both opportunity and fear, to reboot our approach to network security. While there is a growing recognition that visibility into IoT device networks is crucial, the path forward remains a tough balance of investment, innovation, and risk management. The promise of Industry 4.0 is enticing, but the reality of its implementation is fraught with costly challenges that the sector is only beginning to fully appreciate.
7 Lesser-Known Manufacturing Overhead Costs Driving Up Production Expenses in 2024 - HVAC Upgrades Required by New Manufacturing Air Quality Standards
Manufacturers are now grappling with the need to overhaul their HVAC systems to comply with the latest air quality regulations that came into effect in 2024. These new rules demand not just better energy efficiency but also the integration of sophisticated filtration and ventilation systems to enhance indoor air quality. It is evident that the EPA is pushing hard for these improvements, framing them as crucial steps to protect worker health and curb the transmission of respiratory illnesses. Yet, these necessary upgrades come with hefty initial investment costs, a tough financial hurdle for many in the manufacturing sector, particularly when they are already dealing with escalating production costs. Adding to the complexity, the transition to these regulation-compliant HVAC systems is hindered by shortages in the availability of necessary equipment and parts, a consequence of recent shifts in refrigerant standards and other industry-wide changes. The industry is also feeling the pressure from a growing consumer demand for sustainable HVAC solutions. Ultimately, navigating these new standards presents a significant challenge, demanding a balance between regulatory compliance, financial prudence, and operational feasibility.
The Environmental Protection Agency's new National Ambient Air Quality Standards are shaking things up for US manufacturers. The new standards are calling for significant changes to factory air quality, pushing for a serious overhaul of heating, ventilation, and air conditioning systems. They are pushing the use of better filtration, more ventilation and advocating for a multilayered approach to improve indoor air quality, especially in an effort to reduce the spread of respiratory viruses. These standards are not just a gentle nudge, they are more like a firm shove toward cleaner air in industrial settings.
Upgrading HVAC systems to meet these new standards is proving to be quite the undertaking. These new standards require HVAC systems to integrate high-efficiency particulate filters, which are very effective in trapping a wide range of airborne particles. However, these filters increase resistance to airflow, and thus, the systems need more powerful fans that draw more energy. This increased energy use can drive up electricity bills for these facilities. We're not just talking about swapping out a few filters. These systems often require a complete redesign to handle the new refrigerants that are being phased in, which, by the way, is also leading to limited availability of certain equipment and parts. The redesign is not only impacting the availability but also the price, with some reports predicting that newer models compatible with refrigerants like R454B will be more expensive than what we have currently. It is estimated that with these changes there might be a 10-30% increase in energy usage. There is also the need to sanitize and maintain these systems properly which is shortening the lifespan and increasing costs. Moreover, the shift comes with its own set of financial challenges. The initial investment for these upgrades is substantial. Many facilities are also required to do airflow testing after upgrades, which is another often overlooked cost. Companies might need to invest in real-time air quality monitoring systems, which can sometimes cost 40% more than the initial installation of the HVAC system itself. With the complexity of these new systems maintenance costs are expected to increase by 15% or more. There is also a risk of non-compliance fines up to $50,000 per day. While there is talk of long-term savings through reduced energy bills and lower refrigerant costs, the upfront expenses are daunting. The hidden costs are beginning to pile up.
But it is not all doom and gloom. There is a positive outlook. Some data suggests that better air quality could cut down workplace illnesses by around 20%. There is also a claim that investments in these upgrades could pay off in as little as three years. Despite the high initial costs and ongoing expenses, these HVAC upgrades could lead to a healthier workforce. Although, given the patchwork nature of these standards across different regions and the financial hurdles involved, one has to question how effectively these new regulations will be implemented and whether the smaller players will be able to keep up without significant financial strain. It's a complex issue with many moving parts, but one thing is clear: the push for better air quality in manufacturing is changing the game, and it's fascinating to see how this will unfold.
7 Lesser-Known Manufacturing Overhead Costs Driving Up Production Expenses in 2024 - Raw Material Storage Costs Double from Extended Lead Times
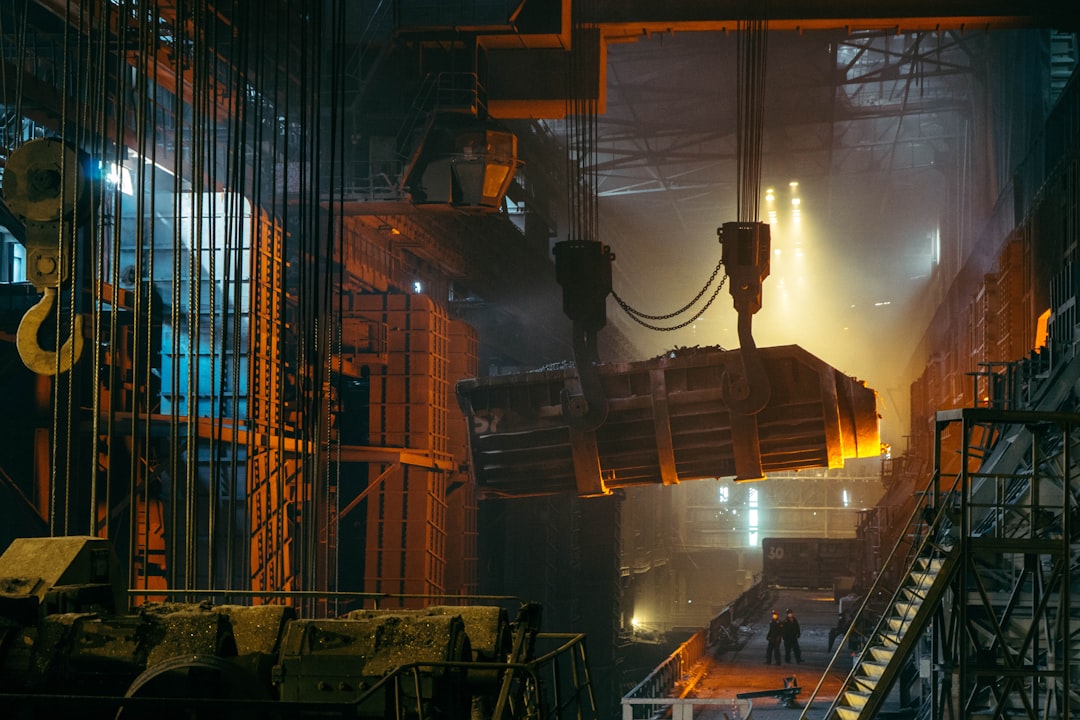
Extended lead times are seriously impacting how much it costs to store raw materials, with expenses doubling in some cases. This is largely due to ongoing supply chain disruptions that show no sign of easing. Manufacturers, in an attempt to keep production lines moving, are forced to order materials far in advance, leading to a significant increase in inventory levels. The result is a need for more warehouse space, and often at a premium, to accommodate the excess stock. The situation is further aggravated by unpredictable price fluctuations of raw materials, adding another layer of complexity to cost management. Companies are finding themselves in a tough spot, having to balance the need for a steady supply of materials against the escalating costs of holding them. Many are questioning whether current inventory strategies are sustainable in the long term, particularly when it ties up capital that could be invested elsewhere. It is a challenging environment, where the ability to accurately forecast demand and optimize storage capacity has become crucial for keeping a lid on overheads. The current scenario underscores the need for more flexible and resilient supply chain strategies that can adapt to rapid changes without incurring excessive storage costs.
It seems that longer lead times are not just a logistical headache but a financial one too, particularly when it comes to raw material storage. What I find intriguing is how this stretches out the time materials sit idle. In many cases, this idle time has effectively doubled the holding costs. These are not trivial expenses, they encompass everything from the physical space these materials occupy to insurance. It is not just about paying rent for warehouse space. We are talking about the depreciation of these materials over time, and even the opportunity cost of having capital tied up in inventory that is just sitting there. In some industries, these costs have ballooned by as much as 50%.
The volatility in raw material prices only makes this worse. The longer these materials are held, the more they're exposed to market fluctuations. Geopolitical tensions, economic factors, and shifts in market demand can cause prices to spike. When these spikes happen, they are not just hitting the cost of the materials themselves but are also compounded by the already inflated storage fees. It's a double hit that can be quite severe.
And then there is the impact on manufacturing strategies, like just-in-time, which is all about efficiency and minimizing waste. Extended lead times force a move away from this, pushing companies to stockpile materials to avoid production delays. This pivot can lead to its own set of problems, such as needing more space and facing more waste if materials become obsolete before they are even used. Every extra week of lead time seems to add around 20% to storage costs. When you think about it, that is a huge burden on budgets that are likely already under strain.
Companies heavily dependent on a few suppliers for specific materials are facing added risks. Any delay on the supplier's end can cause a domino effect, leading to a spike in storage costs as companies stockpile to buffer against these disruptions. It is not just the direct costs either. There is a whole administrative side to managing larger inventories that often gets overlooked. More staff time is needed to track and manage these materials, which means labor costs are going up, diverting resources from other activities that could be adding more value to the business.
The need for more warehouse space is also a critical point. As storage needs grow, companies often have to invest in more real estate, which brings its own set of expenses, from operational costs to property taxes. Insurance premiums go up with the increased volume of stored materials, to cover for potential losses, whether from theft, damage, or just the materials becoming outdated. All of this adds to the operational costs. Finally, there is the strategic angle. With so much capital tied up in managing and storing raw materials, there is less available for innovation and development. Funds that could be invested in R&D are instead being used to cover the costs of excess inventory. This situation might be stifling growth and affecting companies' ability to stay competitive. It is a complex web of interconnected issues, all stemming from extended lead times and impacting various facets of manufacturing operations.
7 Lesser-Known Manufacturing Overhead Costs Driving Up Production Expenses in 2024 - Quality Control Lab Recertification Fees Under Updated ISO Guidelines
With the latest revisions to ISO guidelines, the fees associated with recertifying quality control labs are undergoing notable adjustments, potentially driving up production costs for manufacturers. The updated criteria set by bodies like the Centers for Medicare & Medicaid Services now involve increased user fees for Clinical Laboratory Improvement Amendments. In addition to these escalated fees, laboratories might encounter extra expenses related to compliance follow-up assessments and evaluations. As entities work to meet ISO standards, the necessity of maintaining thorough records and putting into practice robust quality management systems becomes more pronounced, suggesting a possible need for greater investment in measures to avoid the costs of falling short of compliance. This development highlights the wider effect of quality management expenses on manufacturing industries, which are already dealing with increasing operational expenditures.
The buzz around the recent ISO guideline updates is hard to ignore, especially with the chatter about how much it's going to cost labs to get recertified. From what I have gathered, these fees have shot up by as much as 60% in some cases. It seems like it is not just a simple fee hike; it is tied to the increasingly strict compliance hoops that labs have to jump through. The push for more rigorous quality control is evident, but it is raising questions about how sustainable these costs are, particularly for smaller outfits that might not have the deep pockets to keep up.
Then there is the matter of new testing protocols that are being rolled out. Sure, the aim is to boost the accuracy of quality assessments, which is great on paper. But labs are now expected to invest in some pretty niche equipment and get their staff up to speed on these new methods. All of this adds to the time and money spent on recertification, and I wonder how much of this cost is going to trickle down to the manufacturers. It is a bit of a domino effect.
Speaking of manufacturers, they are not just sitting idle during these recertification processes. There are whispers about production schedules taking a hit, with potential downtime while waiting for the all-clear from quality control. This could lead to some serious bottlenecks, not to mention delays in getting products out the door. And let's not forget the risk of hefty fines for those who miss the recertification deadlines – we're talking up to $100,000 a pop. That's a lot of pressure to comply, and quickly.
The paperwork side of things is also getting a bit out of hand. With the ISO revisions, there is a mountain of documentation that needs to be sorted to prove compliance. It is an administrative nightmare, and I am seeing more places either hiring extra hands or buying new software just to keep up with the record-keeping. It is a hidden cost that is definitely adding to the overhead.
Interestingly, some labs are turning to automation to streamline the whole recertification mess. It makes sense, trying to cut down on long-term costs. But, again, there is that initial investment that is not exactly pocket change. I am curious to see how this trend plays out, whether it will actually ease the financial strain or just shift the costs around.
The whole recertification process seems to be at the mercy of the supply chain, too. If labs can't get the materials or equipment they need for testing, it's going to throw a wrench in the works for everyone involved. It's this kind of dependency that can really mess with timelines and budgets.
And with all this talk about global standardization, it's clear that a change in one part of the world can have a ripple effect everywhere else. Companies are scrambling to align with international benchmarks, and it's not cheap. They say there are long-term savings to be had from all this, with a potential return on investment in a couple of years. But it's the upfront costs that are the real kicker.
The market dynamics are also shifting, with quality certification becoming a bigger deal for companies trying to stand out. Those who can't keep up with the ISO revisions might find themselves losing ground to those who can. It's a tough environment, and it underscores just how crucial it is to invest in compliance, not just for the sake of it, but for future growth and staying competitive. The whole situation is a complex tapestry of costs, compliance, and competition, and it is fascinating, if not a bit concerning, to watch it all unfold.
7 Lesser-Known Manufacturing Overhead Costs Driving Up Production Expenses in 2024 - Waste Disposal Surcharges from Stricter Environmental Regulations
Environmental regulations are getting tougher, and it's hitting manufacturers where it hurts – their wallets. Specifically, the cost of getting rid of waste is climbing. As rules tighten around waste management, the fees for disposal are increasing to cover the costs of meeting these new standards. It's not just a simple price hike; the space in landfills is shrinking, making every cubic foot more valuable and expensive. Cities and waste management companies are passing on the costs of new regulatory hurdles, and these surcharges are meant to offset the money spent on adhering to complex environmental laws. These laws require investment in facilities, equipment, and procedures to manage waste more responsibly. With less room to dump trash and more rules on how to do it, manufacturers are feeling the squeeze. The expense of managing solid waste is ballooning, affecting everything from day-to-day operations to long-term financial planning. It is a complex issue with significant financial implications, making it harder for companies to balance environmental responsibility with the economic realities of increased production costs. The situation raises the question of how sustainable these rising expenses are, particularly as they could hinder the growth and financial stability of manufacturing firms.
The tightening grip of environmental regulations is significantly impacting waste disposal costs, particularly through added surcharges. It is quite the puzzle to see how these regulations, while aimed at environmental protection, are reshaping the cost landscape for manufacturers. The core of the issue seems to be the rising expenses associated with compliance, which include not only the direct costs of disposing of waste but also the indirect costs of adhering to a complex web of rules. Landfills, the traditional endpoints for much industrial waste, are becoming scarcer and more expensive to operate, partly due to these very regulations designed to safeguard public health. This scarcity has a ripple effect, pushing up the unit cost of disposal, and it is not just about solid waste, the implications extend to other disposal methods, too, as they are indirectly affected by landfill capacity issues.
Interestingly, waste management providers are implementing environmental surcharges as a means to recoup the costs associated with navigating the labyrinthine regulatory requirements. It appears these surcharges are not arbitrary, they are tied to both operational and capital costs incurred in the process of waste management. Furthermore, the logistical aspect of waste disposal is another area where costs are mounting. With many cities having to transport waste over longer distances to disposal sites, the financial burden grows. This long-haul transportation is not just a logistical challenge, but a significant contributor to increased expenses.
The requirement for licensing, permitting, and the ongoing operation of waste facilities introduces another layer of costs. These are not one-off expenses, but recurring costs that manufacturers must account for, often in the form of surcharges. The situation is indicative of a broader trend where the costs of doing business are increasingly influenced by environmental considerations.
What is particularly noteworthy is the projected increase in production costs for manufacturing firms, directly attributable to these environmental regulations. The data suggests a substantial rise in costs post-regulation implementation, underscoring the financial impact of these rules. Factors such as rising land prices and the costs associated with regulatory compliance are major contributors to this trend, painting a picture of an industry grappling with the dual challenge of environmental responsibility and cost management. The ongoing complexities of managing solid waste, including the operation of collection facilities and material recovery facilities, further compound the issue, adding to the overall increase in production expenses. It is a multifaceted issue where environmental stewardship intersects with economic realities, creating a complex scenario for manufacturers to navigate.
7 Lesser-Known Manufacturing Overhead Costs Driving Up Production Expenses in 2024 - Training Costs for Advanced Manufacturing Equipment Operation
The expense of training workers to use sophisticated manufacturing equipment is a growing slice of the overall cost pie. As factories bring in more advanced machinery, they also need to invest heavily in teaching their workforce how to operate these systems. It is not a one-and-done deal either; ongoing training is crucial as new technologies emerge. The upfront financial commitment is hefty. It seems logical that a well-trained team can boost efficiency and, by extension, productivity. This could, in theory, balance out the training costs over time. But the reality is that manufacturers are in a tight spot, trying to manage these training expenses while also dealing with a general uptick in production costs. It is a bit of a balancing act to stay afloat in the competitive waters of 2024. There is a silent acknowledgement in the industry that these costs are not just about keeping up with the Joneses; they are fundamental to maintaining a skilled workforce. The question is, how effectively can companies absorb these costs without losing their edge? It is a challenging scenario, and the smart manufacturers are the ones who are not just throwing money at the problem but are carefully planning their training investments to align with their long-term strategies. They are the ones to watch, as they navigate this complex financial landscape.
It is interesting to note that the costs associated with training personnel to operate advanced manufacturing equipment are often underestimated. These costs are not trivial. Initial training expenses alone can represent up to a quarter of the total purchase price of new machinery. It becomes even more complicated when considering the ongoing training needs that arise from things like software updates and equipment upgrades. These are not just one-off events, they are continuous, and if not managed properly, the costs can escalate rapidly.
There is also a pressing issue with the skills gap in the industry. Despite all the technological advancements, many employers, about half of them, report a lack of skilled labor. This deficiency is a significant barrier to making the most of advanced manufacturing equipment. It leads to a cycle where companies have to spend more on training, only to find themselves stuck in a loop of inefficiency due to the lack of skilled operators.
The duration of training compared to the lifespan of the equipment is another factor that is often overlooked. Training can take anywhere from 40 to 120 hours, which seems reasonable, but with equipment lasting 10-15 years, the lack of ongoing training is a real concern. It risks obsolescence and inefficiency as technology evolves, which is a critical oversight.
Different industries have varying training costs. Automotive manufacturing, for example, can spend up to 50% more on training than consumer electronics. This disparity is likely due to the complexity and stringent safety regulations in the automotive sector, which require more rigorous and, consequently, more expensive training programs.
The aging workforce is another challenge, with industries facing a projected 30% increase in training costs over the next decade. This increase is tied to the need to train younger employees to replace retiring skilled veterans, a transition that is both necessary and costly.
Adopting simulation technology for training, while beneficial in the long run, can increase initial training budgets by up to 40%. It is a significant upfront cost, although it promises long-term savings by reducing downtime and improving readiness.
Regulatory compliance training adds another layer of expense, increasing the total training budget by about 20%. Failing to adhere to these standards can lead to hefty fines and additional retraining expenses, making compliance a critical, albeit costly, requirement.
The effectiveness of training programs is often not tracked adequately, with nearly 60% of organizations not doing so. This lack of evaluation can result in spending more on ineffective training, leading to poor return on investment and ongoing operational inefficiencies. It is a significant oversight that needs addressing.
Employee turnover exacerbates these training costs. Replacing a skilled operator can cost up to three times their salary, highlighting the importance of engaging and effective training programs to retain talent. It is not just about training, it is about creating an environment where employees want to stay.
Finally, integrating advanced manufacturing equipment with existing systems brings its own set of hidden training costs. Employees often need additional training to adapt to new technologies, which can increase training budgets by as much as 30% for unprepared companies. It is a complex issue that requires careful planning and investment to ensure a smooth transition.
More Posts from mm-ais.com: