7 Essential Phases of the New Product Introduction (NPI) Process A Technical Breakdown for 2024
7 Essential Phases of the New Product Introduction (NPI) Process A Technical Breakdown for 2024 - Market Research and Opportunity Assessment Through Data Analytics
In today's rapidly changing market, understanding consumer needs and identifying potential opportunities is critical for a successful new product introduction (NPI). Data analytics has emerged as a powerful tool for conducting thorough market research and opportunity assessment within the NPI process. By leveraging data, businesses can gain a much deeper understanding of consumer behavior, preferences, and trends. This enhanced understanding fuels more informed decisions related to product design, features, and how to best position the product within the market.
Beyond understanding customer behavior, data analytics allows for a more precise evaluation of the feasibility of new product launches. Previously hidden insights can come to light, which can significantly reduce risks associated with launching a new product. The ability to uncover hidden insights and predict market reactions is increasingly important as competition intensifies. It's crucial for companies to be agile and responsive, and basing decisions on solid data is a key factor in achieving this agility and ensuring long-term success in the NPI process.
In the realm of new product introductions, the landscape is littered with failures, a sobering statistic highlighting the crucial role of understanding the market before committing resources. A large portion of these failures can be attributed to a lack of rigorous market research, making the application of data analytics more vital than ever. Surprisingly accurate predictions of consumer behavior, sometimes exceeding 85%, are achievable using machine learning to sift through the vast trove of historical purchase data and preferences.
The sheer volume of data generated globally, a staggering 90% of which is recent, offers companies an unparalleled opportunity to gather insights for smarter market research. Sentiment analysis allows us to dissect the emotional response consumers have towards products, moving beyond simple opinions to understand feelings, a nuanced perspective that conventional survey methods often miss.
A/B testing, a robust method of experimentation, brings data-driven decision-making into sharp focus, allowing for a clearer understanding of which product features truly resonate with the target consumer group before committing to full-scale production. It's important to note that consumer trust in data handling is paramount. The risk of losing customers due to perceived misuse of their data is significant.
Mobile devices play a pivotal role in modern market research, capturing over half of all web traffic and presenting a unique channel to observe and gather real-time data about consumers' on-the-go choices. Interestingly, by employing predictive analytics, we can optimize market research spending, potentially reducing costs by 30% through a more targeted approach to the most promising markets.
Eye-tracking technology has advanced considerably, offering deep insights into how consumers visually interact with products and marketing materials. It can pinpoint what elements draw attention and what ultimately repels customers, providing a strong understanding of visual engagement.
Neuromarketing, a fascinating blend of neuroscience and marketing, uses brain activity to decode subconscious reactions to products, potentially providing a wealth of information that may remain hidden when using traditional methods. It raises interesting questions about how we subconsciously interact with the things we buy. While the methods are still evolving, they hold promise for future research.
7 Essential Phases of the New Product Introduction (NPI) Process A Technical Breakdown for 2024 - Advanced Engineering Design and Technical Specifications Development
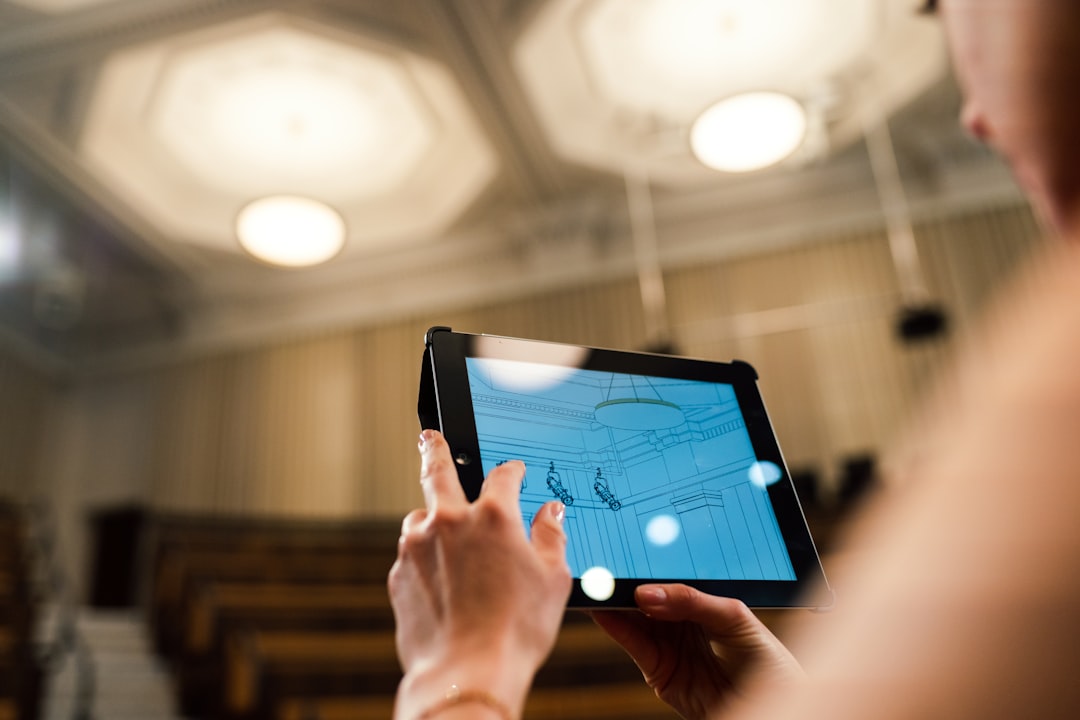
Within the New Product Introduction (NPI) process, the "Advanced Engineering Design and Technical Specifications Development" phase is crucial for bridging the gap between conceptual ideas and a tangible product ready for manufacturing. This stage meticulously translates the product's functional requirements and technical needs into detailed engineering documents that guide the design process. This isn't a one-time activity but an iterative cycle of design, prototyping, and testing to explore and refine potential design solutions. This necessitates a high level of cross-functional collaboration to ensure the design perfectly aligns with the overall product vision, user expectations, and business goals.
The complexity of developing these specifications is undeniable. Engineers face the challenge of incorporating evolving industry standards and future-proofing the product for a dynamic marketplace, particularly given the heightened competitive pressures seen in 2024. Organizations must maintain agility and adaptability within this phase, recognizing the inherent risks associated with insufficient design and specifications that can lead to costly product failures later in the NPI process. Successfully navigating this phase depends on a comprehensive understanding of both the technical and market-driven needs of the intended product.
The phase of developing detailed engineering designs and technical specifications is a crucial step in the NPI process. It's where the initial product concepts, informed by market research, are translated into tangible and functional specifications. We're seeing a rise in the use of parametric design methods, which automate certain design processes, offering increased efficiency and faster iteration cycles. A change in one parameter automatically updates related parts of the design model, allowing engineers to explore design space more quickly.
One of the interesting trends here is the increasing use of concurrent engineering principles. This approach emphasizes early and ongoing collaboration between design, manufacturing, and other relevant teams. This helps avoid issues that could otherwise cause costly delays later in the process. The benefits of collaboration seem evident; a 50% reduction in product development cycles is frequently reported.
The technical specifications themselves are becoming increasingly detailed and rely heavily on advanced simulations. Finite element analysis (FEA), for instance, allows engineers to model and predict how materials will behave under different stresses. This predictive capability enables informed decision-making early on and reduces the need for physical prototypes in some instances.
We're also witnessing the growing adoption of Design for Manufacturability (DFM) principles. These principles aim to simplify the manufacturing process and reduce costs by incorporating manufacturability considerations right from the design phase. There's a potential to lower costs by 20-30% in this way. However, I'm still curious about how these cost reduction claims are measured, especially given potential tradeoffs in other areas.
3D printing, also known as additive manufacturing, has become an essential tool in engineering design. It allows for the rapid creation of physical prototypes, reducing lead times significantly compared to traditional manufacturing methods. It's fascinating how a physical model can be made in a matter of days, which is a remarkable leap from the older methods. The ability to get feedback quickly is an added advantage.
Generative design algorithms are becoming increasingly prevalent, leveraging artificial intelligence to explore a large number of design possibilities based on specified criteria. This is an area where human intuition can be augmented by intelligent machines, leading to innovative designs that may not have been considered otherwise. It is a tool for creativity but I wonder if it also creates a reliance on the automated tool at the expense of intuitive design skills.
The technical specifications, which are the formal record of these engineering design choices, also serve as crucial communication tools. These detailed specifications reduce the chances of misunderstandings between various teams, acting as a unified document that guides all project stakeholders. However, I think we need to be mindful of the balance between overly restrictive specifications and flexibility to accommodate changes during the development process.
The incorporation of virtual and augmented reality (VR/AR) technologies is another trend shaping engineering design. Engineers and stakeholders can explore and interact with product designs in immersive environments, leading to a greater understanding and improved decision-making. It's a great way to visualize the product and share it with stakeholders. Yet, as a researcher, I think we need to be careful about the potential for VR/AR to become the primary method of design communication and potentially neglecting the importance of physical prototyping and hands-on experience.
Regulatory compliance, of course, continues to be a paramount concern in the engineering design process. Any failure to comply with relevant standards can result in severe consequences. Engineers must remain fully informed about all applicable rules and standards throughout the design and development process. It seems that the number of standards and regulations in some areas are increasing which may be contributing to lengthening design cycles.
Lastly, the trend towards modular design offers flexibility and efficiency. This approach makes it easier to upgrade or replace specific components in a product, extending its lifespan and reducing waste. It's a compelling approach to sustainability, but I think it's important to analyze the tradeoffs related to modular design and the potential for increasing the overall product complexity. Also, how well this approach is suited for various product categories is still under investigation.
This phase of advanced engineering design and technical specification development is undoubtedly instrumental in the overall NPI process, ensuring a smooth transition from product concept to successful launch. By embracing these developments, and remaining critical at the same time, the industry can enhance product quality, streamline production, and foster innovation in the future.
7 Essential Phases of the New Product Introduction (NPI) Process A Technical Breakdown for 2024 - Risk Management and Critical Component Sourcing Strategy
Within the New Product Introduction (NPI) process, a robust risk management strategy and a well-defined critical component sourcing plan are crucial. As companies increasingly rely on global supply chains, understanding and mitigating the associated risks becomes paramount for ensuring the quality and timely delivery of products. This requires a thorough evaluation of potential suppliers, considering factors like reliability, production capacity, and their ability to handle changes in demand or unforeseen events. Moreover, companies need to anticipate risks proactively, paying close attention to both their internal processes and the external marketplace. This proactive approach fosters resilience and flexibility, allowing companies to react effectively to changing circumstances. By aligning comprehensive risk management with strategic sourcing decisions, companies can protect their NPI initiatives, ultimately setting the stage for successful product launches. It's a critical step in ensuring that the product vision translates smoothly into reality.
In the intricate dance of bringing a new product to market, risk management and securing vital components emerge as critical considerations, especially in the current dynamic environment of 2024. It's striking how heavily reliant some industries are on a single supplier for crucial parts, with a staggering 80% of supply sometimes coming from a single source. This creates a vulnerability, as any disruption at that source could significantly impact the product's launch or even its continued availability. We need better ways to understand and mitigate these risks.
Market fluctuations can throw a wrench in the works, leading to price hikes in raw materials and potentially a 5-15% increase in the total cost of producing the product. I think a more dynamic approach to risk assessment would be beneficial for companies, allowing them to respond quickly and potentially avoid huge budget overruns.
Then there are the unpredictable, global-scale events like the recent pandemic or geopolitical issues. These have the ability to disrupt supply chains for extended periods, even months. I've been studying research that suggests a shift towards localized sourcing or diversifying the supplier base could be a way to cushion the impact of such disruptions, creating a more resilient supply chain.
Interestingly, I've also come across advanced analytics that can proactively identify potential vulnerabilities before they even become a problem. AI-powered solutions are demonstrating the ability to sift through information from different sources and predict supply chain disruptions with a surprising accuracy, well over 90%. These technologies might be able to offer better insight.
Another thing that has caught my eye is how often supply chain interruptions are rooted in a single point of failure. Studies show that about 70% of them are due to a single problem within a supplier or a logistics chain. It's a clear indication that having a firm grasp of the various connections and assessing the risks related to crucial components could yield more reliable sourcing strategies.
I've seen research indicating that partnering with suppliers on risk management efforts can reduce disruptions by about 30%. These collaborations can lead to a flow of information and a more agile response to unforeseen challenges. It's a fascinating illustration of how cooperation can contribute to more resilient systems.
One thing that's always been a concern is the push for the cheapest possible components. While tempting, it often comes at a cost. A focus on low-cost sourcing without a commensurate focus on quality and reliability can easily lead to product recalls, which can quickly surpass 25% of the initial development cost. A balanced approach is needed, with a healthy understanding of the risks and the consequences of choices.
Navigating regulatory complexities is another hurdle that many businesses face. It appears that over 40% of companies struggle to manage these intricate regulations, and this often leads to delays. This points to the importance of a proactive sourcing approach that includes thorough compliance checks, which can help streamline operations and reduce these types of interruptions.
It's also noteworthy that businesses have varying risk appetites when it comes to sourcing. Some are willing to sacrifice low prices for reliability, while others favor low costs even if it potentially weakens the long-term relationship with their supplier. This makes me wonder if there's a need for clear communication about risk appetites to foster stronger partnerships.
Emerging technologies like blockchain are showing promise in securing supply chains and ensuring the traceability of parts, but adoption rates are still relatively low, below 20%. It seems that these technologies have a lot of potential and could significantly enhance risk management within sourcing strategies. It would be interesting to see how quickly adoption rates increase in the future.
Overall, risk management and secure component sourcing are a key aspect of successfully bringing a new product to market. Given the constantly shifting dynamics of the marketplace, embracing both traditional and innovative approaches to risk mitigation can ultimately increase the chances of success for new product launches.
7 Essential Phases of the New Product Introduction (NPI) Process A Technical Breakdown for 2024 - Manufacturing Process Setup and Quality Control Implementation
Within the NPI journey, the "Manufacturing Process Setup and Quality Control Implementation" phase is crucial for translating the meticulously crafted designs into real-world products while upholding the highest quality standards. This stage involves setting up efficient manufacturing systems, providing thorough training to personnel, and configuring assembly lines that precisely match the product's technical specifications and market demands.
Equally important is the implementation of a strong quality control framework that incorporates both proactive measures to prevent defects and reactive methods to identify and address issues that do arise. These measures are essential for ensuring product quality, catching potential problems early in the process, and ultimately safeguarding customer satisfaction and the company's brand reputation.
The consequences of overlooking this stage can be severe, resulting in costly product recalls and damage control efforts that can derail a product's market success. In a world of increasingly sophisticated consumers and heightened competition, a smoothly functioning production process and robust quality control aren't just desirable—they are essential components of effective risk management and a well-executed NPI strategy. Neglecting these elements can severely undermine the overall goals of a new product introduction.
Within the NPI journey, setting up the manufacturing process and implementing effective quality control are critical steps that often get overlooked. While the initial focus is on design and concept validation, seamlessly transitioning to production requires careful planning and a robust quality framework. Interestingly, the origins of modern quality control methods like Statistical Process Control (SPC) date back to the 1920s, thanks to the work of Walter Shewhart. Shewhart highlighted that most quality problems stem from flaws in the production process itself, not necessarily defects in the products themselves. It's a reminder that a process-focused approach is vital.
The costs associated with poor quality can be staggering. Some studies indicate that companies could be saving up to 10 times the cost of poor quality if they had proper quality control practices in place. This makes a strong case for investing in quality systems, even though the initial costs might seem daunting. The costs of poor quality can include customer dissatisfaction, product recalls, rework, and lost sales. It is estimated that it can cost manufacturing companies 15% or more of their overall revenue, emphasizing the high stakes involved.
Furthermore, manufacturing setup time is a crucial factor impacting efficiency. If done correctly, the setup time can be significantly reduced, sometimes even by 90%, resulting in shorter lead times and increased output. Methods like Lean manufacturing and SMED (Single-Minute Exchange of Die) are examples of how companies can dramatically improve efficiency by minimizing the time needed to switch between production runs. It's fascinating how much difference a streamlined setup process can make.
In 2024, quality control is increasingly intertwined with technology, especially with the rise of real-time data analytics and the Internet of Things (IoT). Companies employing these techniques have observed reductions in defect rates of over 60%, and they are able to address quality issues much faster. This technology can be extremely helpful in monitoring the process and making timely adjustments. Yet, we must remember that human errors continue to contribute significantly to quality problems, accounting for as much as 70% of issues. While automation and advanced quality control systems can reduce reliance on human judgment, training and well-defined procedures are still important to mitigate human error as much as possible.
Quality management frameworks like Six Sigma have gained popularity, as they emphasize data-driven decision-making in reducing defects. Companies that fully embrace the Six Sigma approach have seen improvements in profit margins by an average of 20-30%, showcasing its effectiveness. Furthermore, AI and machine learning are enabling companies to predict quality issues with surprising accuracy, about 85%, potentially avoiding waste and improving consistency in production. It's a compelling illustration of how intelligent systems are helping to improve quality.
The quality of incoming materials and parts from suppliers also plays a critical role in the overall quality of a finished product. Companies that partner with suppliers on quality initiatives have noticed a 25% decrease in defects in those parts. This reinforces the idea that quality isn't just a responsibility within a single company's walls but a collaborative effort across the supply chain. Interestingly, establishing a strong quality culture within a company can have a remarkable impact on customer satisfaction. Organizations with this type of culture have seen a four-fold increase in customer satisfaction. It's a powerful example of how a company's commitment to quality can benefit its overall brand reputation.
The manufacturing process setup and quality control implementation phase represents a crucial step in transforming the product design into a reliable, market-ready offering. Companies must not only ensure the processes are efficient but also embed a culture that prioritizes quality at every step. By leveraging innovative technologies and collaborating with partners, businesses can not only optimize the production process but also significantly improve the probability of successful product launches in the competitive landscape of 2024 and beyond.
7 Essential Phases of the New Product Introduction (NPI) Process A Technical Breakdown for 2024 - Product Testing and Performance Validation Protocols
Within the New Product Introduction (NPI) process, establishing "Product Testing and Performance Validation Protocols" is crucial for ensuring a product's readiness for the market. These protocols define a series of tests and assessments to verify that the product aligns with its intended functionality, technical specifications, and, importantly, customer expectations. This phase incorporates a range of testing methodologies, from basic functionality checks to rigorous stress tests that aim to expose potential weaknesses or flaws before widespread release.
The increasing use of advanced technologies, like sophisticated simulation software and data analysis tools, has revolutionized the testing and validation process. These advancements allow engineers to scrutinize the product's performance under a wide variety of conditions, leading to a much deeper understanding of aspects like durability, usability, and safety. The insights gained from these tests are invaluable in iterating upon product designs and manufacturing processes, which often leads to improvements in both quality and efficiency.
However, striking a balance between comprehensive testing and time-to-market is a continuous challenge for companies. Excessively lengthy testing protocols can delay product launch, potentially giving competitors an advantage in a fast-moving market. Companies must carefully consider the potential risks associated with insufficient testing and the costs associated with a delayed launch.
Ultimately, rigorous product testing and performance validation protocols serve as a crucial safeguard against potential product failures in the market. These processes reduce the risk of expensive recalls or negative publicity due to malfunctioning products. Thorough testing is an investment that builds both customer trust and brand reputation over the long-term.
In the realm of new product development, the phase dedicated to product testing and performance validation is often a critical point where many products either succeed or fail. Surprisingly, research indicates a substantial portion—around 60% to 70%—of products that fail in the marketplace do so because of inadequate testing protocols. This highlights a potential blind spot in numerous NPI processes, where the importance of rigorous validation is sometimes overlooked. It's a stark reminder of how vital robust testing practices are to minimizing failure rates.
One interesting aspect of testing is how consumer feedback plays a significant role in shaping the final product. During the testing phases, it's not uncommon to see roughly 70% of product modifications directly influenced by customer input. This underlines the immense value of incorporating real-world perspectives during testing. This feedback can be invaluable for identifying areas needing improvement and ensuring the product aligns with actual consumer needs before reaching the market. It's also a great example of how the NPI process can become a cycle of continuous improvement through testing.
While the initial investment in robust testing might seem high, it often yields a compelling return on investment. By proactively identifying and addressing potential issues through comprehensive testing, businesses can prevent costly recalls and maintain product reliability in the field. This can lead to a return that is as much as 50 times the initial testing investment. It's a testament to the idea that investing in quality upfront can be significantly more cost-effective than dealing with failures later in the product lifecycle.
The integration of automation into testing has fundamentally changed validation protocols. Automated testing systems have allowed for a substantial reduction in testing time. Some companies report completion of testing cycles up to 80% faster than traditional methods. This not only leads to more rapid iterations but also accelerates the product's path to market, enabling a quicker response to market dynamics. Yet, with increased automation it can sometimes become difficult to ensure thoroughness, making human oversight still crucial.
Navigating the regulatory landscape for product testing can be challenging. Non-compliance with testing standards can lead to significant financial penalties, with fines reaching into the millions of dollars depending on the industry and the severity of the non-compliance. This emphasizes the need for engineers and product development teams to stay abreast of current standards and regulations throughout the design and validation process. There are ongoing debates about whether the number of regulations are increasing and if this is causing delays in product development.
Virtual simulations and digital twin technologies are making significant inroads into performance validation. This shift is enabling engineers to gain insights into product performance under diverse operating conditions with higher accuracy compared to physical prototypes. One benefit of this approach is a reduction in prototyping costs of around 30%. It is intriguing how this technology is rapidly changing the landscape of testing. It's important to note that simulations are based on models, and real-world behavior can still be unpredictable.
It's increasingly evident that involving multidisciplinary teams in performance validation can lead to better outcomes. The diverse perspectives and backgrounds of these teams often help in detecting and resolving complex issues. Research suggests that engaging diverse groups can decrease product development complexities by about 40%. It can also ensure that testing is more comprehensive.
Integrating continuous feedback loops during performance testing can also lead to significant improvements in product performance metrics. By iteratively incorporating feedback throughout the testing process, teams can refine and enhance the product based on actual user interactions rather than solely relying on theoretical scenarios. Studies have shown that this approach can improve performance metrics by as much as 25%, underscoring the value of continuous learning and iteration. This approach does require that the project team be receptive to feedback and make the appropriate changes.
One critical aspect of validation is lifecycle testing. This involves understanding how the product will perform over its intended lifespan. It's a sobering realization that around half of all product failures occur after launch rather than during the initial testing phase. This illustrates the importance of designing and testing for the long-term use cases and conditions the product will encounter. Addressing these potential issues through early identification and mitigation can significantly contribute to product longevity and customer satisfaction. More robust testing may be needed for products with long lifespans, which might add cost and time.
A quality-first culture has a tangible impact on the success of product launches. Companies that prioritize quality assurance during testing have consistently seen a correlation with higher success rates. These organizations have achieved launch success rates that are roughly double that of competitors who may not have a strong quality focus. This reinforces the importance of cultivating a company culture that prioritizes quality throughout the NPI process. This culture is easier to foster in some industries and company environments than in others.
The product testing and performance validation phase is a critical component of the NPI process. By acknowledging the importance of robust testing protocols and implementing these methods in an informed way, organizations can better navigate the complex landscape of product development and substantially increase the chances of launching successful products in the dynamic market of 2024. There are still unanswered questions about how to best balance the time and cost of testing with the risks of launching a product that has not been tested thoroughly.
7 Essential Phases of the New Product Introduction (NPI) Process A Technical Breakdown for 2024 - Supply Chain Integration and Distribution Network Planning
Within the New Product Introduction (NPI) process, effectively planning and integrating the supply chain and distribution network is vital to bridge the gap between manufacturing and reaching the market. This phase necessitates strong collaboration across all parts of the supply chain, including suppliers, manufacturers, and logistics providers. The aim is to ensure a smooth transition from product development to market launch, avoiding the common bottlenecks and disruptions that can delay or complicate new product introductions.
In today's market, customers have come to expect fast and reliable delivery, and companies must adapt their logistics strategies to match those expectations. This requires a careful evaluation of existing distribution networks and a willingness to adjust as needed. Failure to account for market changes and optimize delivery can lead to delays, increased costs, and frustration within the overall NPI effort.
Businesses that have a well-designed and well-managed supply chain and distribution plan can often build a competitive edge through faster and more reliable delivery. It's becoming more important to achieve this as competition intensifies in many industries. While the initial effort can require significant planning and coordination, the potential rewards can be significant for long-term success in a changing market. The alternative – not planning well for distribution – can be costly in many ways.
In the context of introducing a new product in 2024, effectively integrating the supply chain and planning the distribution network is a critical step that can easily be overlooked. While the initial stages often focus on design and concept development, ensuring a smooth transition to production and delivery requires a more holistic approach.
The intricate nature of today's global supply chains is undeniable. We're seeing that a significant portion of supply chain disruptions, perhaps as much as 70%, stem from a single point of failure. This emphasizes the need for careful consideration and potentially restructuring the network to avoid relying on any one supplier or route. It's a sobering reminder that even seemingly minor issues in one part of the network can cause wider problems.
One interesting trend is the distribution of costs within supply chains. A substantial amount, around 80%, of a company’s logistics expenditures can often be traced back to just a small fraction (20%) of its suppliers. This suggests that paying attention to those key supplier relationships and strengthening those partnerships could provide considerable cost reductions and increase the efficiency of the entire supply chain. This may even mean changing the number of suppliers for certain components to gain more leverage.
The use of intelligent algorithms and optimization techniques in distribution planning is also increasingly prominent. It’s quite remarkable that using these algorithms can often lead to a 30% reduction in delivery times. These faster deliveries not only contribute to improved customer satisfaction, but they also translate to improved operational efficiency and a competitive advantage in the marketplace. We need to understand the limits of these tools in specific applications and be mindful of the potential for unintended consequences.
Another crucial aspect is the importance of cross-functional collaboration within the organization. Studies show that those companies that prioritize effective communication and knowledge sharing between supply chain managers and sales teams experience a notable improvement in order fulfillment rates, as much as a 50% increase in some cases. This suggests a reduction in silos and better integration between functions can result in stronger supply chain management overall.
We're also seeing a significant shift in companies adopting real-time tracking technologies. Interestingly, companies using these technologies can potentially achieve reductions of stockouts by about half. This capability to monitor inventory levels and track the progress of shipments provides companies with highly relevant information to optimize their distribution processes. However, concerns about privacy and the security of data will need to be addressed as these technologies become more widespread.
In this consumer-driven market, it's vital to acknowledge the significant emphasis consumers place on the delivery experience. Around three-fourths of customers are willing to pay extra for a smoother and more convenient delivery. This clearly indicates that adapting distribution strategies to meet these consumer expectations is not only a good idea, but it could provide a distinct competitive edge.
The use of predictive analytics is also impacting distribution networks. Businesses that employ predictive analytics to forecast demand have seen an improvement in accuracy of over 85%. This enables better inventory management and aligning distribution strategies with real-time market changes. This is an exciting area but the accuracy of predictive models depends heavily on the quality and quantity of the data that is fed into them. We also need to remember that unforeseen events can still dramatically change market conditions.
Another factor to consider is the cost of a poorly functioning supply chain. In some cases, it can surpass 50% of a company’s total revenue. It’s a striking indicator of how important it is to establish and maintain robust supply chain practices and optimize each function of the process.
The location of distribution centers also significantly impacts the cost of goods and supply chain logistics. Careful consideration of the location of warehouses and distribution centers can result in a 10% reduction in costs, as well as reductions in transport times and fuel consumption. It's quite fascinating how something seemingly simple as the location of a warehouse can have such a large effect.
Finally, the ongoing digital transformation across industries, known as Industry 4.0, has led to a substantial increase in investment in supply chain technologies like IoT and blockchain. Over two-thirds of companies are making such investments. This highlights a critical shift towards a more connected and transparent supply chain that adapts more quickly to dynamic market conditions. However, it will be interesting to see the degree to which the adoption of these technologies truly transforms the industry.
In summary, optimizing supply chain integration and distribution network planning is integral to the success of introducing a new product. By acknowledging these emerging trends and fostering a culture of collaboration and innovation, companies can build resilient supply chains that are not only effective but also more responsive to the demands of the modern consumer market in 2024 and beyond. There's still much we don't know about how these technologies will impact industries in the future.
7 Essential Phases of the New Product Introduction (NPI) Process A Technical Breakdown for 2024 - Market Launch Strategy and Post Release Performance Tracking
The "Market Launch Strategy and Post Release Performance Tracking" phase within the New Product Introduction (NPI) process is crucial for ensuring a new product not only reaches its intended audience but also performs as expected after launch. Developing a strong market launch strategy involves understanding your target customers, identifying the best ways to communicate with them, and knowing how your product compares to competitors. It's also important to manage customer expectations from the start to minimize potential disappointment.
After the launch, monitoring how your product is doing is vital to understand its success and improve future products. This includes looking at sales numbers, customer reviews, and how people are interacting with your product in the marketplace. This information can then be used to adjust marketing strategies and refine product features. Companies need to be adaptable and prepared to change direction quickly based on the real-time data they're gathering, as the marketplace is constantly changing. Setting clear performance goals from the beginning can help in making smart decisions throughout the launch and beyond, guaranteeing the product's long-term success and continued relevance in a dynamic environment. It's a constant process of evaluating, adjusting, and adapting to stay ahead of the game.
The idea that being the first to market with a new product automatically leads to success is often overstated. Research shows that a significant number of market leaders weren't the first ones to introduce a similar product. This suggests that a strong marketing approach and careful execution might be more important than just getting there first.
After a product's release, staying connected with customers and using data analytics to understand how they're using the product can make a difference in customer retention. Companies that do this have reported improvements in retention rates of up to 25%. By watching how the product is actually used in real-world settings, it gives companies a path towards making future products even better.
Social media buzz around a new product can have a strong impact on sales. It appears that products which receive at least a thousand mentions on social media during the first week of launch can see an increase in sales of up to 15%. This is a clear example of how effective community-driven marketing approaches can be.
Return rates for a product can also give you a sense of whether or not people are satisfied with it. Products with return rates below 10% tend to have happier customers, while those with return rates higher than 20% seem to indicate a mismatch between what customers expect from the product and what it actually does. This underscores the importance of testing and validating the product thoroughly before it’s ever released.
When trying to understand if a product is doing well after it's launched, companies can use predictive analytics to gain more accurate insights into how the market will change over time. With predictive analytics, these companies report an accuracy of over 80%. This means they can make changes to their marketing plans and keep the product relevant in the market for a longer period.
One might expect that A/B testing is a technique that is only used during the initial stages of development. It's interesting that companies which continue to do A/B testing of their products for six months after launch often identify aspects that significantly improve the user experience and customer satisfaction ratings. These increases can be as high as 30%.
Taking the time to gather and respond to customer feedback during the product development process can improve the quality of future product releases. A substantial majority of companies (nearly 60%) that integrate real-time feedback into their development cycle see improvements in the later versions of their products. This reinforces the point that tracking performance after a product is released is an important aspect of continuous improvement.
Investing in resources for customer support after a product is launched can yield a high return in the long run. It's not uncommon to see customer loyalty and repeat purchases increase by 20 times the original investment in post-launch support. This indicates that ongoing communication and support are essential for maintaining a strong market position.
After a product is on the market, changing prices based on how the product is selling can have a noticeable effect on the total sales. Companies that modify their pricing strategies within the first quarter after launch based on product performance data have reported an increase in sales of up to 50%.
Visual representations of product launch metrics can help make it easier to make informed decisions after a product is launched. Companies that use visual dashboards to track performance often see an improvement in their ability to respond and make changes by as much as 40%. This highlights the importance of clear and readily available data to make well-informed decisions after a product is launched.
While there are still many things to consider and questions to answer regarding the relationship between product release and marketing performance, the insights above highlight the growing importance of carefully developed market launch plans and using data to continually evaluate product performance. In an increasingly competitive environment, proactively gathering and responding to data is a critical factor for success in the long term.
More Posts from mm-ais.com: