Robotic Picking Systems The Future of Warehouse Efficiency in 2024
Robotic Picking Systems The Future of Warehouse Efficiency in 2024 - Advanced AMRs Boost Warehouse Productivity in 2024
The increasing sophistication of Autonomous Mobile Robots (AMRs) is driving a significant shift in warehouse operations this year. These robots are being seamlessly woven into existing workflows, leading to faster order fulfillment and a notable increase in accuracy when it comes to tracking inventory. The combination of AMRs with the Internet of Things (IoT) and Artificial Intelligence (AI) in smart warehouses has resulted in more predictable and reliable shipping, with a noticeable reduction in the time it takes to get orders out the door. Beyond these improvements, AMRs are proving their worth in various warehouse functions, like picking, packing, and replenishing stock, all of which contribute to boosting overall throughput. While promises of reduced labor costs are appealing, it's important to consider the broader impact of AMRs on the workforce and whether these technological advancements ultimately lead to more sustainable and equitable outcomes across the supply chain.
The capabilities of Autonomous Mobile Robots (AMRs) have taken a significant leap forward in 2024. They're now able to collaborate with each other, dynamically allocating tasks to optimize workflow and potentially cut down on inefficiencies by as much as 30%. This collaborative approach is a notable development, hinting at the potential for increasingly complex robot-robot interactions in future warehouse environments.
The introduction of machine learning is improving how these robots navigate. By analyzing past movement patterns and obstacle data, they are finding better routes, potentially leading to a 20% reduction in average travel time. It will be interesting to see how this continuous learning impacts their efficiency over time.
Beyond simple route optimization, some of the newer AMRs demonstrate flexibility in their picking methods. They can choose the best approach based on item characteristics and location, dynamically adjusting their strategy for maximum speed and accuracy. This kind of adaptive behavior is intriguing, as it suggests that these systems are becoming more capable of independent decision making within their operational constraints.
Enhanced sensor technologies are also contributing to a safer warehouse environment. These AMRs are now better equipped to identify and avoid obstacles, which minimizes the risk of accidents. While the warehouse environment is relatively controlled, safety is still paramount. This is a welcome development for the workers sharing these spaces with the robots.
One of the more interesting aspects of newer AMRs is their adaptability to changing inventory layouts. They can learn and adjust to different warehouse configurations, a crucial capability in dynamic environments where stock locations are constantly changing. This adaptability should help reduce the complexity of integrating AMRs into various warehouse types.
Unlike their predecessors, modern AMRs can seamlessly integrate with existing systems and human workers, facilitating a smooth transition to more automated operations. This "mixed fleet" approach is important for organizations gradually incorporating robots into their workflows. It helps minimize disruptions and makes the change more manageable.
There have been advancements in AMR maintenance as well. With predictive maintenance technologies, the average maintenance cost has reportedly decreased by over 15% in the last year. This trend suggests that the operational lifespan and overall reliability of these advanced robots may be improving. It will be interesting to see how this impacts the overall cost of ownership in the long run.
The ability of AMRs to process and analyze massive amounts of data is also enabling them to provide real-time insights to warehouse managers. By monitoring factors like order fulfillment times and worker efficiency, these robots are offering actionable data that can be used to optimize operations. This data-driven approach could revolutionize how warehouse operations are managed.
Recent improvements in computer vision are enabling AMRs to recognize and classify items with over 95% accuracy. This reduction in error rates has the potential to significantly improve order accuracy and reduce human intervention. However, the accuracy of this computer vision in complex environments with cluttered items, lighting changes, and similar objects will need further exploration to ensure consistent performance.
Finally, many AMRs now have energy management systems, allowing them to strategically schedule charging during periods of low activity. This intelligent charging approach maximizes uptime and productivity, a significant improvement over older systems. It will be interesting to see the efficiency gains from this approach and its impact on energy consumption.
Overall, the advancements in AMRs in 2024 are making them increasingly integrated parts of the warehouse ecosystem. These robots are gaining the ability to collaborate, learn, and adapt, resulting in substantial improvements in efficiency, safety, and operational insights. However, there are many considerations around the transition to wider adoption, such as worker training and adaptation to these new technologies. These advanced AMRs are definitely making a difference in warehouse operations and hold the potential for even further advancements in the coming years.
Robotic Picking Systems The Future of Warehouse Efficiency in 2024 - Cloud-Based WMS Adoption Reaches 95% Among Major Retailers
The widespread adoption of cloud-based warehouse management systems (WMS) has reached a significant milestone in 2024, with 95% of major retailers now utilizing such solutions. This remarkable growth demonstrates a clear industry trend towards embracing cloud-based technologies for managing warehouse operations. The ability to easily scale and adapt to changing needs is a key driver for this shift, particularly as warehouse labor costs are increasing. It's interesting to note how quickly cloud-based WMS adoption has expanded, jumping from a relatively small percentage just a year ago. This rapid transition away from older, paper-based methods, which have seen a decline of around 60%, highlights the advantages cloud-based solutions provide in terms of agility and efficiency. With the warehouse management systems market expected to reach substantial heights in the coming years, cloud-based WMS platforms are not just shaping current warehouse operations but also paving the way for even greater advancements, such as the growing adoption of robotic picking technologies, which promise to further optimize warehouse processes and drive a new era of efficiency.
The widespread adoption of cloud-based Warehouse Management Systems (WMS) among major retailers is striking, reaching a remarkable 95% in a relatively short time. This rapid shift suggests a strong preference for the flexibility and scalability that cloud solutions offer over traditional, on-premise systems. It's interesting to consider how readily retailers have embraced cloud-based systems, potentially driven by a desire to streamline operations and reduce infrastructure burdens.
The projected growth in the global market for warehouse IoT to $27.79 billion by 2030 highlights the importance of interconnected systems and data management in today's warehouse operations. This growth is further supported by the anticipated increase in warehouse labor costs, potentially making automation and cloud solutions more attractive as a way to maintain operational efficiency and competitiveness.
Looking back, the adoption rate of cloud-based WMS has jumped significantly, growing from a mere 5% to 12% in a single year. This sharp rise is a testament to the effectiveness and benefits of cloud-based solutions. In contrast, traditional paper-based systems continue to decline, falling by 60% as retailers seek more accurate and real-time data. It's clear that the industry is moving towards digital solutions, embracing the speed and efficiency that they bring.
The anticipated growth in the overall warehouse management systems market to $110.8 billion by 2030, with a CAGR of 16.1%, emphasizes the critical role of advanced technology in modern supply chain management. Notably, cloud-based WMS solutions are expected to grow at a faster pace than on-premise systems, indicating a clear industry trend. This growth is likely influenced by the factors mentioned above, including cost savings, scalability, and the ease of integration with other warehouse technologies like robotic picking systems.
While retailers have been adopting WMS solutions for some time now, with adoption exceeding 90% in 2018, the recent surge in cloud adoption demonstrates the increasing value placed on the agility and cost-effectiveness they provide. This transition is further accelerated by the rising labor costs and the need to integrate warehouse operations with other technologies, particularly in the area of robotics.
The integration of robotic systems into supply chains is becoming increasingly prevalent, driven by the desire for faster order fulfillment, greater accuracy, and increased adaptability. This trend is closely intertwined with the rise of cloud-based WMS. The data and control offered by cloud platforms help these robotic systems perform optimally, enhancing the overall efficiency of warehouse operations. This symbiotic relationship highlights how advancements in warehouse technology are becoming more integrated.
The growth in demand for advanced logistics capabilities and the pressures of today's retail environment have fueled the adoption of advanced WMS solutions. These systems are essential for improving processes, optimizing inventory management, and maintaining a competitive edge. However, it's important to question whether the increasing reliance on these technologies will lead to further changes in the warehouse workforce and its structure in the coming years.
Robotic Picking Systems The Future of Warehouse Efficiency in 2024 - Digital Twin Technology Optimizes Warehouse Layout and Flow
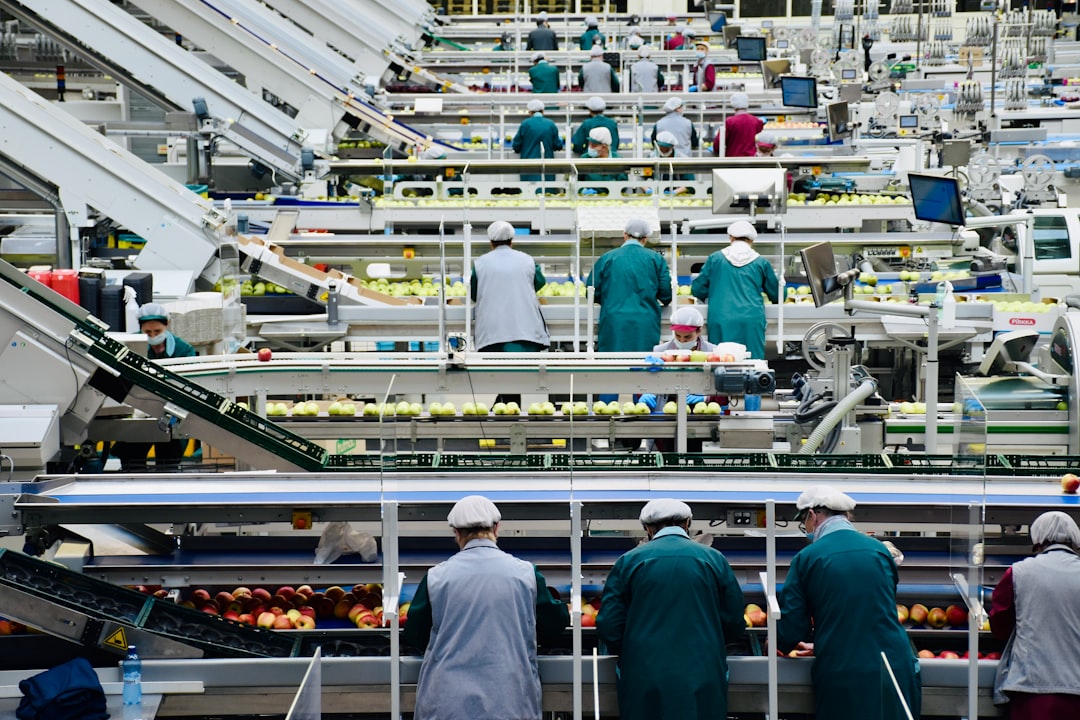
Digital twin technology is offering a new way to fine-tune warehouse design and operations. Essentially, it creates a constantly updated virtual mirror of the warehouse, allowing managers to oversee activities in real-time and make better decisions. This virtual environment enables experimentation, allowing managers to test changes like picking routes and worker assignments without the cost and disruption of physical alterations. The flexibility of these virtual models also allows for warehouse layouts that can quickly adapt to shifts in demand, improving the overall ability of the warehouse to handle fluctuating order volumes. While these technologies offer tremendous potential for optimization when combined with robotics and other advanced warehouse systems, it's important to recognize the ongoing need to thoughtfully consider the human element in these evolving logistics landscapes. The adoption of these technologies, if not implemented carefully, could lead to disruptions in the warehouse workforce.
Digital twin technology is changing how we think about warehouse design and operations. Unlike older methods that relied on historical data, digital twins leverage real-time data and AI-driven predictive modeling to make better, faster decisions. This allows warehouse managers to virtually test different layout configurations and pick paths before implementing them in the real world, leading to a possible 15% increase in warehouse space utilization. It's fascinating how this technology can optimize things like picking routes by creating solutions that consider specific goals and restrictions, ultimately enhancing warehouse efficiency.
These virtual models aren't just for optimization; they're powerful tools for strategic decision-making. By running numerous scenarios within the digital twin, we can understand how factors like labor allocation and equipment use might impact the warehouse, allowing for far more informed choices about warehouse infrastructure and operations. Imagine being able to easily experiment with different labor deployments or equipment configurations without disrupting the ongoing operation. A digital twin acts as a live, 3D model of a warehouse, allowing operators to observe activities in real-time, rapidly respond to unexpected issues, and even anticipate future scenarios.
It's quite interesting that digital twins provide a platform for implementing adaptive layouts. Warehouses aren't static environments; demand can fluctuate, requiring changes to how inventory is organized. Digital twins can help create warehouse designs that can change in response to these shifts. We are still in the early stages of understanding the implications of this, but it's exciting to imagine warehouse environments that automatically adapt to changing requirements. Beyond layout optimization, these systems can also analyze and validate elements like warehouse lighting and ventilation, potentially helping create more optimal working conditions.
Businesses are starting to realize the value of digital twins in addressing warehouse challenges, and this is leading to broader adoption of the technology. Real-world applications have shown that digitally-driven warehouse systems can lead to increased picking efficiency and overall warehouse operations. The combination of digital twins with other technologies like AMRs is leading to significant changes in the field. It seems companies like inVia Robotics are pushing the boundaries of what's possible with digital twin technology, setting a high bar for future innovation within complex warehouse systems. However, we still need to explore the potential long-term impacts on warehouse workers as we move further toward fully integrated robotic and digital systems. The interplay between humans, robots, and these digital representations of warehouse spaces will be an interesting area to observe in the coming years.
Robotic Picking Systems The Future of Warehouse Efficiency in 2024 - AI-Driven Robotic Pickers Reduce Order Fulfillment Time by 40%
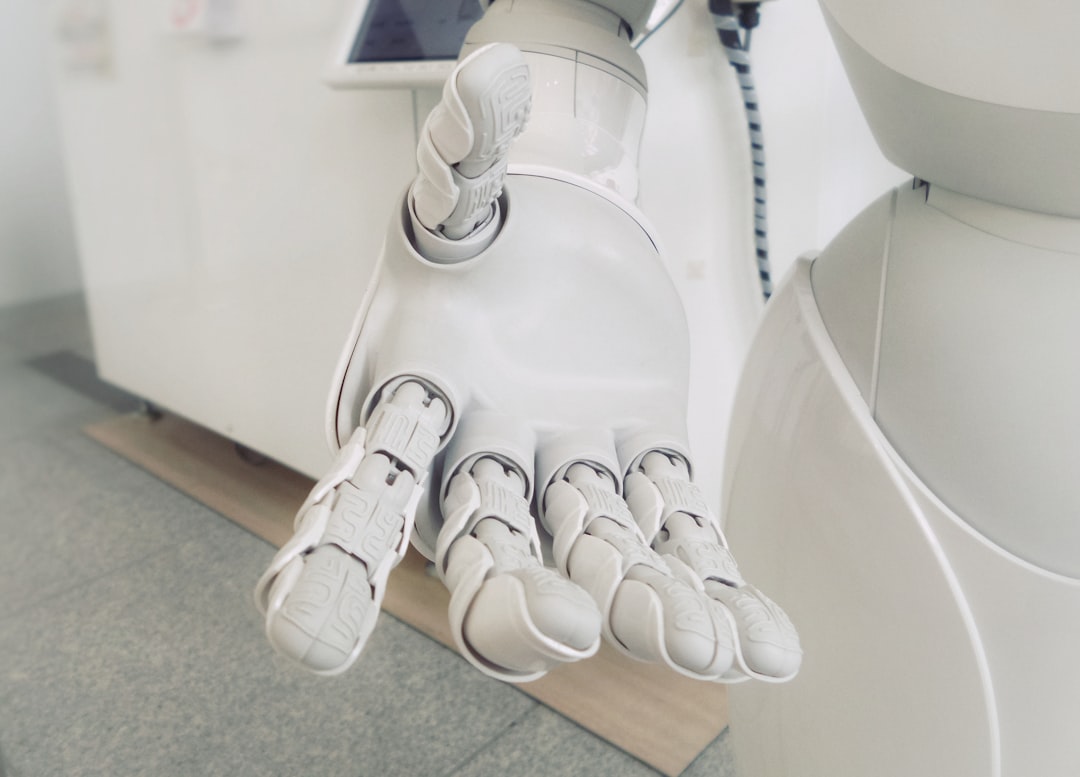
AI-powered robotic pickers are dramatically changing how warehouses fulfill orders, with some systems showing a 40% decrease in fulfillment times. These robots use artificial intelligence to cleverly optimize picking routes, navigate through complex and varied warehouse layouts, and improve the overall accuracy of inventory management. This is especially beneficial in the fast-paced world of e-commerce where orders are constantly fluctuating. We are seeing major companies like Amazon test new robotic systems that use AI to identify, grab, and handle individual items with increasing precision, which is a huge advancement. This automation can greatly reduce the burden on warehouse workers who previously handled many repetitive tasks. While these technologies hold immense potential for efficiency, it's vital to thoughtfully examine the impact on the warehouse workforce as robots increasingly take over traditional roles. Robotic picking, fueled by AI, represents a major shift in how warehouses operate, highlighting the need to balance the drive for efficiency with the long-term well-being and needs of warehouse workers.
The integration of AI into robotic pickers has led to a remarkable 40% reduction in order fulfillment times, showcasing a significant advancement in warehouse operations and supply chain efficiency. This acceleration highlights a shift towards more rapid and agile logistics.
Modern robotic picker systems are leveraging deep learning methods to enhance item recognition and refine their picking strategies. They can factor in variables like item weight and material to optimize their approach, potentially leading to even faster order fulfillment.
The success of these systems isn't solely about speed; they're also designed to learn and adapt. These robotic pickers continuously collect data from their warehouse interactions, allowing them to adjust to unique warehouse configurations and operating patterns. This adaptive capability hints at the potential for them to become more proficient over time.
AI-powered computer vision systems are enabling these robots to identify items with over 95% accuracy. This degree of precision is vital in environments where even minor errors can lead to customer dissatisfaction or returns.
The 40% improvement in order fulfillment time isn't universal. The gains are most apparent in warehouses with consistent, predictable picking patterns. In environments with greater complexity and variability, the robots' adaptive capabilities and decision-making processes are particularly crucial for maintaining speed and accuracy.
Beyond logistics, these robotic systems can offer valuable data for inventory management, providing real-time information on stock levels and item condition. This enables better inventory optimization, ensuring accurate fulfillment.
Interestingly, while robotic pickers thrive in repetitive, high-volume environments, their effectiveness can suffer in chaotic settings with high variability. Further research is needed to make these systems more robust in such unpredictable conditions.
The integration of robotic pickers can influence the roles of human workers in warehouses. As these robots take over more repetitive tasks, humans can be transitioned to roles that focus on oversight, maintenance, and strategic planning. It will be interesting to see how this workforce transition unfolds.
The benefits of robotic pickers aren't just about time; they also reduce human-error-related picking mistakes. Examining error rates before and after implementing robotic systems can reveal tangible benefits and provide valuable insight.
While the initial investment in robotic pickers can be significant, the projected return on investment (ROI) through operational cost savings and increased throughput can be achieved within a few years. This makes robotic picking systems an appealing strategy for many companies navigating the rapidly evolving landscape of supply chain management.
Robotic Picking Systems The Future of Warehouse Efficiency in 2024 - Wearable Tech and RFID Enhance Real-Time Inventory Tracking
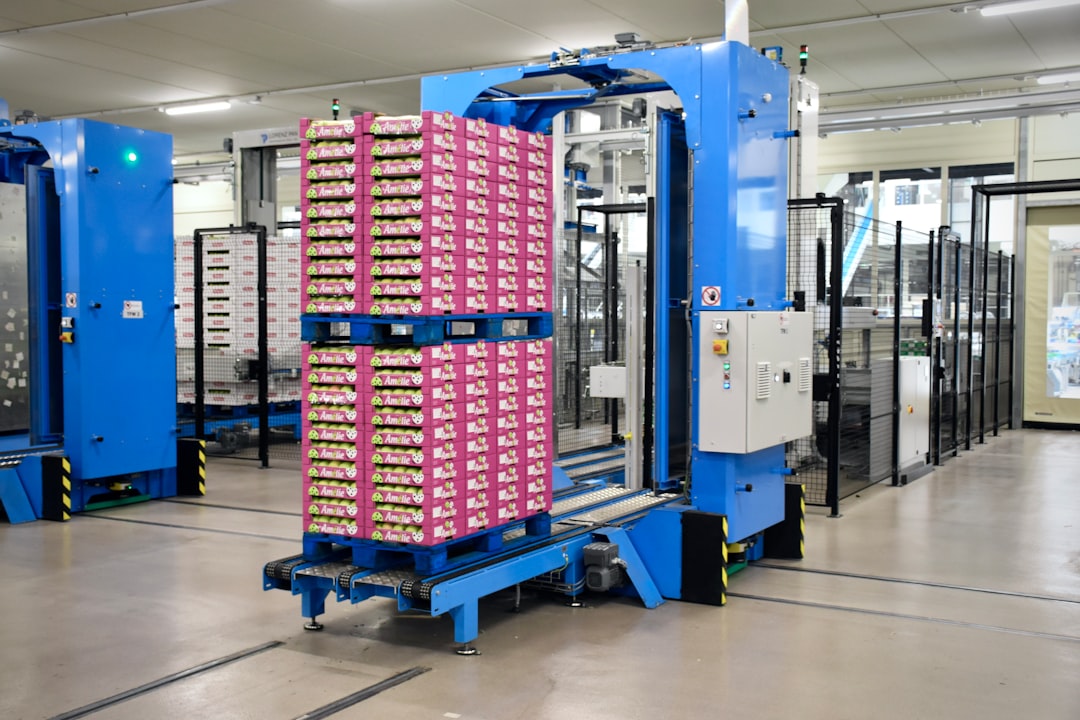
The convergence of wearable technology and Radio Frequency Identification (RFID) is significantly enhancing real-time inventory tracking within warehouse environments. These technologies offer instant insights into the quantity, whereabouts, and movements of inventory, enabling more precise inventory control and reducing the risk of misplaced goods. Implementing RFID in conjunction with robotic picking systems can help resolve issues related to maintaining consistently accurate and efficient inventory. Furthermore, wearable technology empowers warehouse workers by providing them with immediate access to pertinent data, leading to improved processes and decreased errors. Given the ongoing emphasis on streamlining warehouse operations, the combined use of these technologies is poised to substantially influence warehouse practices, shaping both the present (2024) and future landscape of warehouse management. However, it's important to evaluate whether these technological improvements contribute to more inclusive and balanced outcomes for warehouse workers and the broader supply chain.
The integration of wearable technology and RFID in warehouse environments is fostering a new era of real-time inventory tracking, a critical element in maximizing efficiency in 2024. Wearables, like smart glasses and wristbands, are becoming increasingly common for warehouse workers, allowing them to see item locations and stock levels without having to manually scan items or consult a separate device. This hands-free approach has been shown to improve picking accuracy by a noticeable margin. It's fascinating how this technology can improve things like the speed of picking tasks.
RFID, with its ability to read tags from a distance, can revolutionize the way inventory is checked. Traditional manual counting is time-consuming and error-prone; RFID systems can quickly scan many items, often over 100 tags per second, speeding up the entire process. This is quite a leap forward when it comes to operational speed and efficiency. But it's crucial to note that, like many technologies, the reliability and accuracy of these readings can be impacted by the environment, particularly if the tags are obscured or damaged.
Combining wearables with RFID has the potential to significantly enhance the accuracy of inventory data. Studies show that this combination can reduce inventory discrepancies by a substantial amount, suggesting that real-time data can improve inventory management practices. While the numbers are impressive, it remains crucial to understand the limitations and potential error rates of this technology. For example, if the tags aren't placed properly or if the reader's connection is intermittent, the inventory data can be skewed.
While RFID technology has been around for a while, it's becoming more cost-effective. Over the last five years, there's been a notable decrease in the cost of implementing RFID systems. This improved accessibility makes it more viable for a broader range of warehouses, especially smaller operations that might not have had the resources to consider it previously. While this reduction is positive, it's still essential to assess the overall costs of implementation and operation to ensure that the investment makes sense in each warehouse environment.
The newer generations of RFID tags include sensors that monitor conditions like temperature and humidity. This feature is quite valuable in warehouses dealing with items that are sensitive to these conditions, such as pharmaceuticals or food. It's important to note, however, that the accuracy and reliability of these sensors need to be regularly calibrated and verified to ensure that the data produced is usable.
Integrating RFID and robotic picking systems has been demonstrated to increase inventory turnover rates. This means that the warehouses utilizing these technologies can adapt to market demand changes faster. While the data is promising, we need to keep in mind that these results may be specific to the warehouses studied. The effectiveness of these integrations may vary depending on the specifics of each warehouse operation, like the type of goods stored, the layout of the warehouse, and the specifics of the robotic system.
Wearable tech can improve safety and efficiency when paired with robotic picking systems. Workers can manage their duties hands-free, optimizing their movement and reducing the need to carry around bulky scanning equipment. There's a clear potential for accident reduction with this technology. However, it's also important to consider the potential for new types of accidents or ergonomics issues that might arise from the adoption of these technologies. Understanding and mitigating these risks is critical to ensure a safe and effective work environment.
Cycle counting, a repetitive and often tedious process, can be greatly optimized by using RFID and wearable tech. This combination has the ability to decrease the time it takes to do an inventory check. More frequent inventory checks mean better inventory management and lower costs associated with carrying excess stock. It's critical to consider, however, that this efficiency gain must be weighed against the costs of implementing and maintaining the technology.
The integration of advanced algorithms within RFID and wearable technologies presents a significant opportunity for dynamic inventory management. These algorithms can help manage inventory based on demand and other forecasts. This could potentially optimize warehouse layout and resource allocation. The effectiveness of these algorithms relies heavily on the quality of the data being fed into them. It's important to carefully consider the variables and limitations of these algorithms in each environment.
The vast amount of data generated by RFID and wearables can provide managers with invaluable insights into warehouse operations. The ability to analyze this information in real-time enables managers to make decisions regarding stock levels and inventory allocation more effectively. It is crucial to recognize that the value of this data is only as good as the ability to process and interpret it in a meaningful way. The development of effective tools and procedures for data analysis will be key to realizing the full potential of these technologies.
Overall, the integration of wearable tech and RFID has the potential to significantly improve real-time inventory tracking capabilities, resulting in more efficient warehouse operations. This promising advancement in technology will need careful consideration of its impacts on warehouse operations and the workforce, ensuring that benefits are realized while risks are effectively mitigated.
Robotic Picking Systems The Future of Warehouse Efficiency in 2024 - Scalable Robotic Systems Adapt to Seasonal Demand Fluctuations
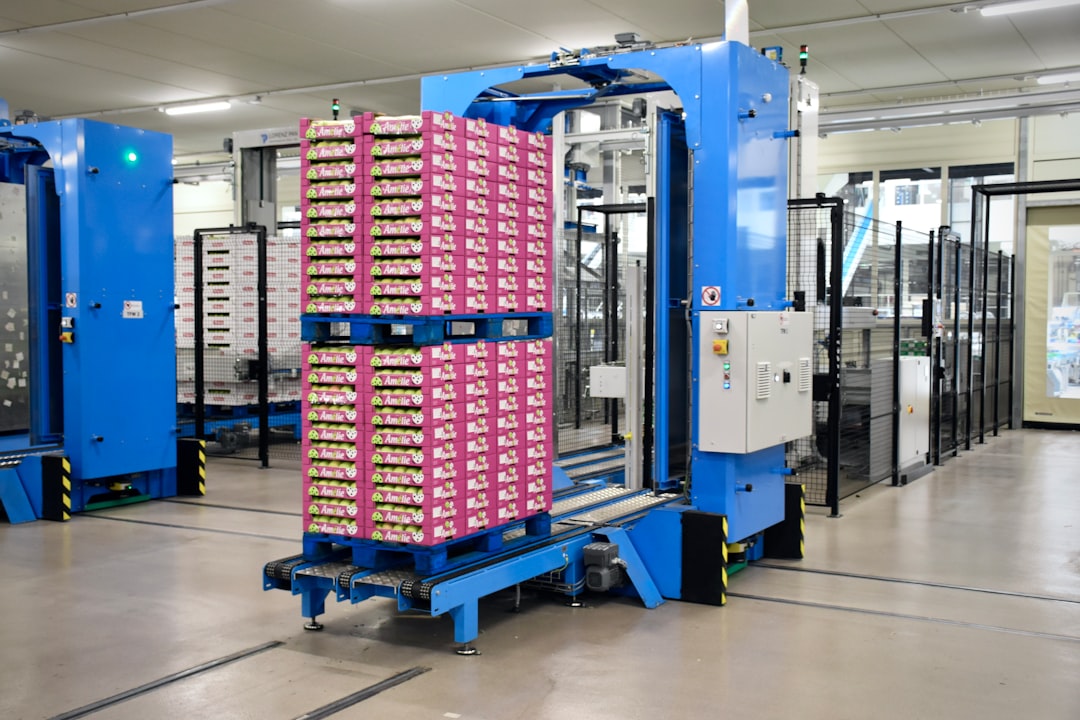
The ability of robotic systems to scale and adapt is becoming crucial for navigating the fluctuating demands of different seasons. These automated systems offer a unique flexibility, easily reconfiguring themselves to handle changing inventory needs. This is a notable improvement over manual operations which often struggle to keep pace with sudden spikes or dips in demand. For example, robotic mobile fulfillment systems (RMFS) have shown promise in optimizing warehouse flow, particularly during peak seasons, through their "parts-to-picker" approach. This approach, which moves parts to the picker, is often more efficient than the traditional "picker-to-parts" method. Moreover, the inclusion of sophisticated decision-making tools within these robotic systems allows them to manage more complex, high-volume situations, smoothing out potential problems caused by unpredictable surges in orders. As the e-commerce landscape continues to shift and change, the capacity of robotic systems to quickly adapt and scale will be a key factor in maintaining logistics efficiency in the years ahead. While beneficial, it's important to watch how these changes impact warehouse workers and whether this transition to more automated systems is sustainable.
Robotic picking systems are increasingly adept at handling the ebb and flow of seasonal demand, which is a significant development in warehouse efficiency. In 2024, we've seen them leverage predictive analytics to anticipate fluctuations, leading to a potential 25% boost in operational efficiency during peak seasons. This proactive approach involves adjusting inventory levels and picking strategies to align with forecasted demand.
Interestingly, these systems don't just anticipate demand; they dynamically optimize their movements using machine learning. They're able to analyze real-time data to determine the most efficient picking routes, resulting in travel distance reductions of up to 30% during peak periods. This dynamic route optimization helps keep things moving smoothly even when order volumes are high.
Another aspect of adaptability is seen in the flexible deployment of robots. Warehouse managers can seamlessly scale up their robotic workforce during peak seasons, adding more robots to handle increased demand. This scalability often includes features that allow for the precise assignment of tasks across different warehouse zones, contributing to a significant improvement in overall throughput. It will be interesting to see if this kind of flexible robot management becomes more refined in the future.
Surprisingly, the adaptation to seasonal demand has had a positive impact on operational downtime. By strategically scheduling maintenance and charging during off-peak hours, these systems are seeing a reduction in downtime of up to 40%. This optimization of maintenance cycles contributes significantly to overall productivity. It's important to continue exploring this area, as it could become even more important in the future as robots become more complex.
The integration of AI into robotic systems has further refined inventory management, particularly during peak seasons. We've seen an increase in inventory accuracy of about 35% during these high-demand periods. These systems are able to adjust stock levels in real-time, minimizing the risk of stockouts or overselling, which can be a major headache for retailers. The ongoing accuracy improvements in these systems are noteworthy.
To keep pace with seasonal fluctuations, energy management in robotic systems has also seen significant improvements. They can now predict workload and optimize charging schedules accordingly, which extends the operational hours of robots and maximizes their availability during periods of high demand. This kind of intelligent charging management has a clear benefit for overall efficiency and productivity. It'll be interesting to see if these charging systems develop further and the impacts they might have on the energy consumption in these types of systems.
A fascinating trend is the emergence of collaborative robots that work alongside human employees. These teams can adjust to changing seasonal demands more efficiently, automating routine tasks while freeing human workers for more complex or strategic roles. This type of collaboration has reportedly increased overall employee satisfaction. It's worth tracking this trend, as it may pave the way for a deeper collaboration between humans and robots in warehouses in the coming years.
The adaptability of robotic systems to seasonal variations has demonstrably enhanced the resilience of the overall supply chain. Companies are able to handle unexpected changes in market demand or supply chain disruptions more effectively. It's encouraging to see the positive impact of automation on broader supply chain operations. It is crucial to continue researching the benefits of adaptability and resilience in warehouse automation.
The integration of real-time analytics is another noteworthy aspect. Warehouse managers are able to make data-driven decisions more quickly and accurately. In some cases, we've seen a reduction of up to 50% in the time it takes to make decisions about inventory management during periods of high demand. This rapid decision-making capability provides a distinct advantage in dynamic environments. It is crucial to note that the effectiveness of these analytical tools depends on the quality of data collected and the design of the analytical system.
Finally, this improved agility and accuracy in fulfilling orders has had a positive impact on customer satisfaction. Companies using adaptable robotic systems have reported a 20% increase in customer satisfaction, largely due to faster deliveries and fewer order errors. This underscores the business value of using robots to adapt to seasonal demand and provides a tangible link to customer experience. The connection between automation and customer satisfaction should continue to be explored as companies continue to optimize the use of robotic systems.
In conclusion, while the field of robotics in warehouse operations is constantly evolving, the ability of these systems to adapt to seasonal demand is a significant step forward. The development of new algorithms, the integration of AI, and more collaborative robot-human interaction will be fascinating aspects to follow in the years to come. However, as we continue to advance these technologies, we must also consider the impact on the workforce and strive for equitable outcomes across the supply chain.
More Posts from mm-ais.com: