Mastering the Formula A Step-by-Step Guide to Calculating Total Variable Cost in 2024
Mastering the Formula A Step-by-Step Guide to Calculating Total Variable Cost in 2024 - Understanding the Components of Total Variable Cost
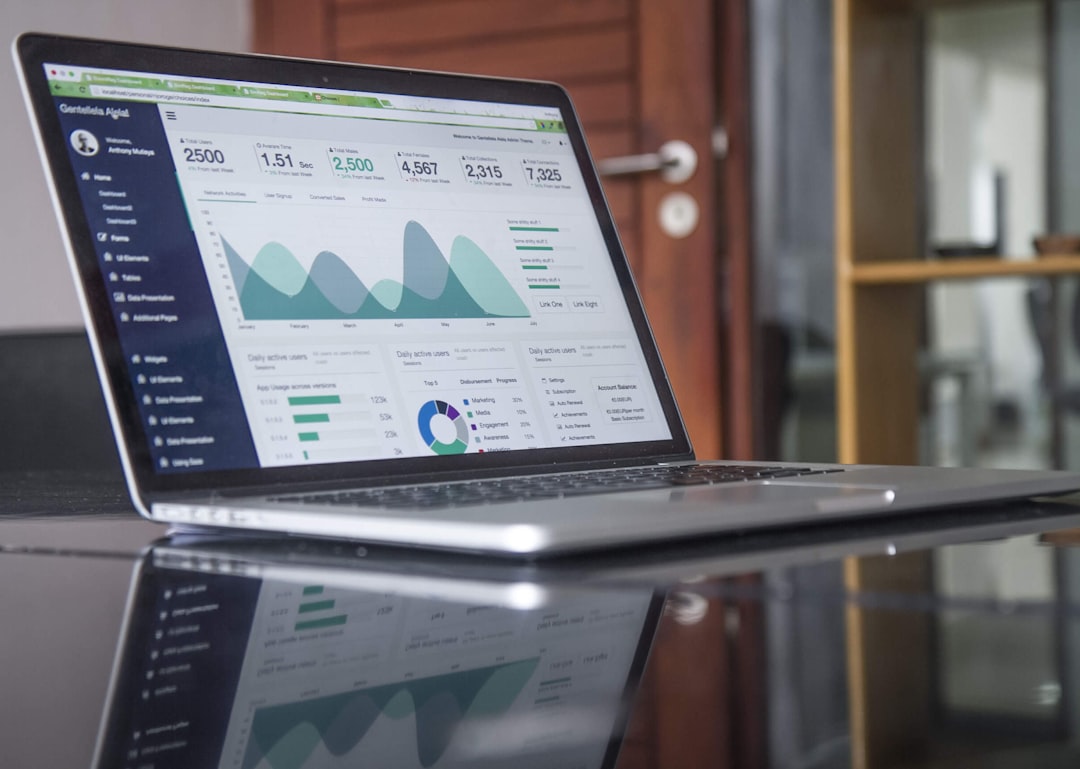
To truly grasp Total Variable Cost (TVC) and its impact on your business, you need to understand its building blocks. TVC is essentially the sum of all costs directly tied to the level of production. This means that as you make more of your product, these costs rise, and conversely, they decrease when production falls. Examples of these costs include things like the raw materials used in manufacturing and the labor directly involved in the production process. Recognizing how these costs behave is key, as they can dramatically affect a business's bottom line. Further, understanding how average variable cost (AVC) is calculated using TVC is helpful in seeing how efficiently your production is generating output. This is a crucial part of understanding how your business is performing, particularly when facing shifting levels of production. In essence, a deep understanding of the components of TVC is vital for businesses hoping to make sound financial decisions and adapt effectively to changing market conditions.
1. The total variable cost (TVC) is highly sensitive to changes in production volume, making it crucial to understand the nature of this relationship, particularly for businesses with substantial fixed costs. It's not a simple, linear relationship and needs careful consideration.
2. Labor, a major part of TVC, isn't just wages. Things like overtime, worker training, and how efficiently the workforce operates can all affect it. These factors are often left out of simpler calculations, leading to possible inaccuracies.
3. The cost of materials, a large portion of TVC, changes with supplier agreements, market conditions, and even global political situations. This volatility makes it essential to have a clear understanding of how it affects production costs.
4. The idea of economies of scale is directly related to TVC. As output increases, the average variable cost per unit tends to go down. This can lead to big cost savings in the long run.
5. If a company makes different types of products, each one can have its own cost structure. This makes figuring out the overall TVC for the entire operation more complex.
6. Using technology in manufacturing can have a big effect on TVC. New equipment might initially make variable costs higher, but long-term efficiency gains can bring those costs down.
7. Seasonal changes have a major impact on TVC, especially for things like farming and retail, where demand goes up and down. This leads to noticeable differences in variable costs depending on if it's a busy or slow time of year.
8. How the production process is designed impacts the calculation of TVC. Highly automated processes are likely to have lower variable costs compared to those that depend more on human labor.
9. It's important to distinguish between direct and indirect variable costs. Indirect ones are sometimes overlooked and could lead to incorrect financial analyses if not identified.
10. Costs that aren't easily quantified, like how supplier relationships affect variable costs, are often not considered in calculations, but they still have a big effect on overall expenses.
Mastering the Formula A Step-by-Step Guide to Calculating Total Variable Cost in 2024 - Breaking Down the Formula TVC = VCu x Q
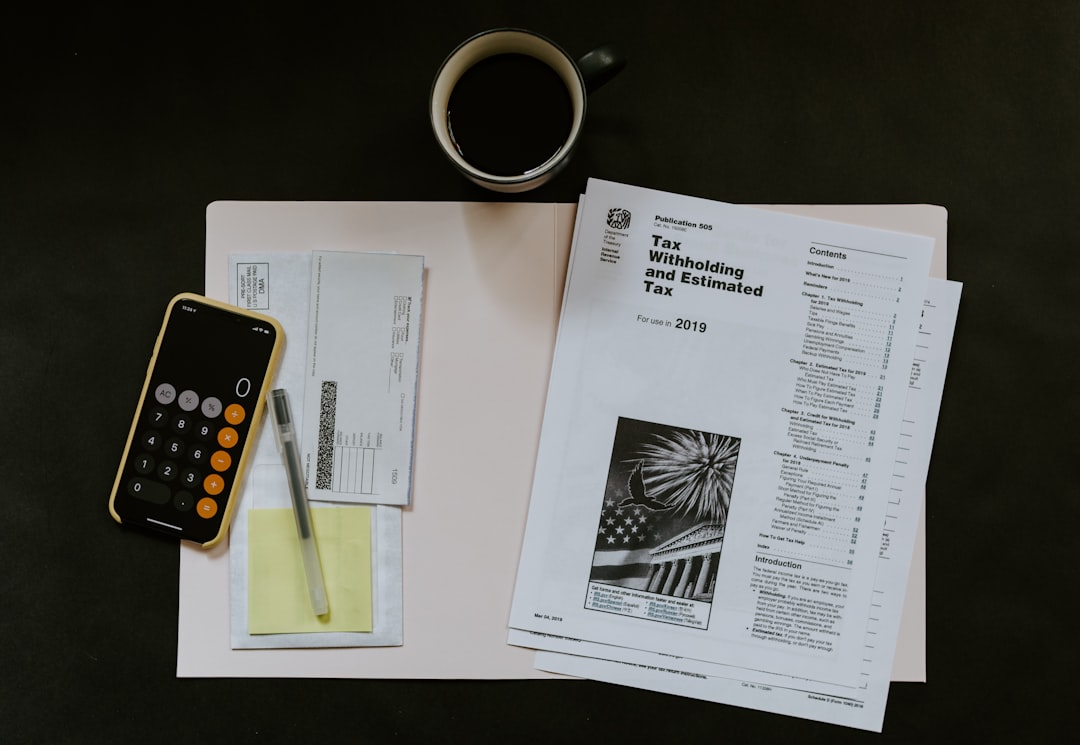
The formula TVC = VCu x Q is fundamental to understanding how total variable costs behave. TVC, or total variable cost, is calculated by multiplying the variable cost per unit (VCu) by the quantity produced (Q). This formula underscores the direct link between production volume and the expenses associated with it. Things like raw materials, labor directly involved in production, and other costs that shift with production levels are captured here. By understanding how these costs move in relation to production, businesses gain a clearer picture of their cost structure and can adapt their strategies more readily. This knowledge becomes particularly important when businesses encounter situations like fluctuating market demands or need to refine their operations for maximum profitability. It provides a powerful tool for making sound financial decisions.
1. **Variable Cost's Dynamic Nature**: The formula TVC = VCu x Q reveals that total variable cost (TVC) isn't simply a straight line response to changes in production quantity (Q). We often find that changes in production volume don't lead to perfectly proportional shifts in TVC. This nonlinear relationship needs to be carefully examined, especially for companies with a large fixed cost base, as it can be a source of unexpected cost changes.
2. **Labor Beyond Wages**: It's easy to fall into the trap of thinking labor costs in TVC are solely wages. But in reality, things like worker training, turnover rates, and variations in worker efficiency all influence the true cost of labor. Simplifying our labor cost estimations by ignoring these aspects might lead to inaccuracies in our overall TVC calculations.
3. **Material Costs and External Shocks**: Material costs, a key component of TVC, can be very volatile. Supplier contracts, market swings, and even global events can have a huge impact on raw material prices. It's crucial that businesses frequently re-evaluate their TVC calculations as even small changes can cascade into significant financial impacts.
4. **Scale and Diminishing Returns**: Economies of scale, where increased production lowers average variable cost per unit, isn't always a guaranteed outcome. As production ramps up, there might be a point where adding more resources doesn't result in a proportional increase in output, a principle illustrated by the law of diminishing returns. This makes accurately predicting TVC more complex in situations where this phenomenon plays a role.
5. **Multiple Product Lines**: When a company produces multiple products, each with a unique variable cost structure, the calculation of total TVC gets considerably more involved. A more detailed and nuanced approach to financial analysis is required because the overall TVC will be a composite of different cost profiles.
6. **Technology's Double-Edged Sword**: Implementing new technologies in production often leads to a short-term spike in TVC due to capital expenditures for equipment. However, if done correctly, those investments can lead to long-term improvements in efficiency and, therefore, significant drops in the average variable cost per unit. This longer-term picture is vital when evaluating TVC in the presence of technology upgrades.
7. **Seasonal Shifts and TVC**: Sectors like agriculture and retail see very strong seasonal swings in demand, making their TVC equally volatile. Planning for these fluctuations is critical, and businesses in these sectors need to have financial strategies that can adapt to these dynamic conditions.
8. **Production Design and Cost Impact**: The specific structure of a production process has a direct effect on TVC. Highly streamlined designs tend to generate lower variable costs by minimizing wasted resources and enhancing resource efficiency. Understanding these design-related cost drivers is important when making changes to production lines.
9. **Direct vs. Indirect Variable Costs**: In our analysis of TVC, we need to distinguish between direct variable costs, like raw materials and direct labor, and indirect variable costs, which are things like variable overhead expenses. It's vital that we don't miss these indirect costs during calculations, as this can lead to incomplete and potentially misleading financial outcomes.
10. **Supplier Relationships and Hidden Costs**: The nature of a company's relationships with its suppliers can create 'hidden' costs not typically captured in a standard TVC calculation. For example, if a company is very dependent on a particular supplier, they might face less leverage during negotiations and pay higher prices than if they had more options. These aspects of supplier dynamics can subtly impact overall expenses but are rarely explicitly accounted for in basic TVC analyses.
Mastering the Formula A Step-by-Step Guide to Calculating Total Variable Cost in 2024 - Identifying Common Variable Costs in Modern Businesses
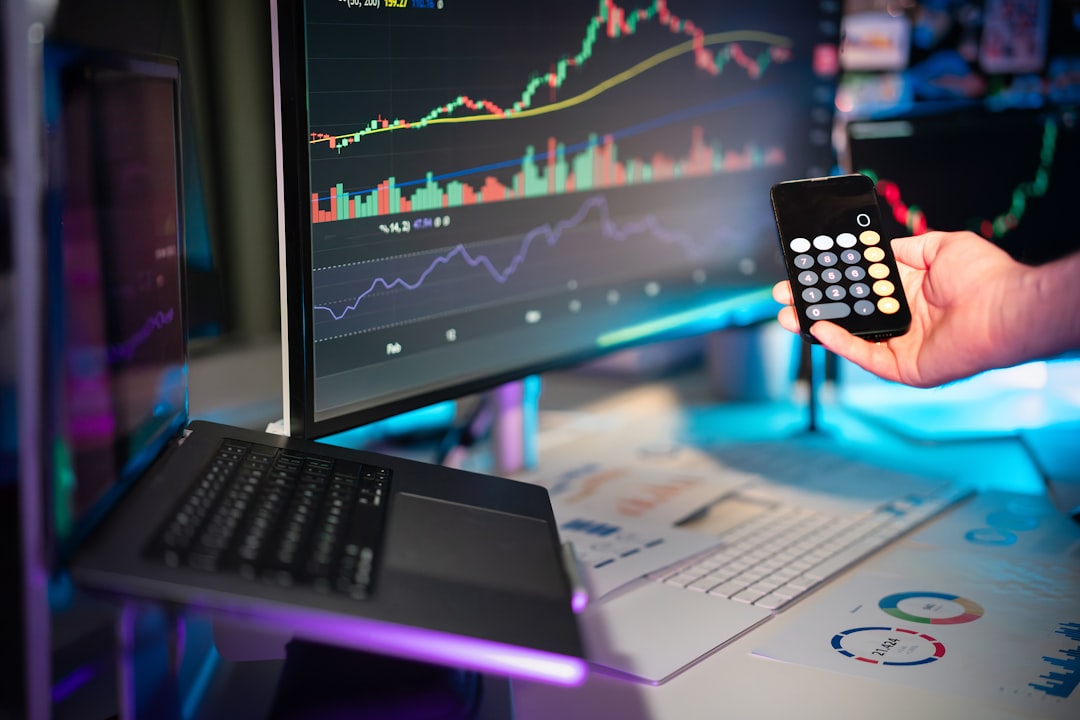
In today's dynamic business environment, understanding and managing variable costs is essential for success. These are costs that directly respond to changes in production levels, encompassing things like the raw materials needed to make products, the direct labor involved in production, and other costs tied to output. It's crucial to remember that these costs are not static; they change based on market fluctuations and production demands. This can lead to major shifts in a company's finances if not managed carefully.
Businesses need to pay close attention to these costs, actively monitoring and analyzing them. This ongoing evaluation helps them make informed decisions regarding product pricing, production efficiency, and overall business strategy. Companies operating in industries with strong seasonal shifts or facing evolving economic conditions must be especially attuned to variable costs. By consistently identifying and tracking these costs, organizations can achieve a clearer picture of their financial situation, improving their ability to navigate the complexities of their operations and ultimately, strengthen their financial outcomes. However, accurately capturing these costs in the face of complexities like indirect variable costs, volatile material costs, or fluctuating labor costs can be challenging and requires a nuanced approach.
1. **Variable Cost Proportionality**: While we often think of a direct relationship between output and total variable cost, the reality is more complex. As production scales up, things can get less efficient, potentially leading to unexpected jumps in TVC, particularly for those companies who already have a large amount of fixed costs they have to cover.
2. **Beyond Wages: The Full Cost of Labor**: When looking at the TVC component of labor, we shouldn't just think of hourly wages. Things like training programs, keeping staff, and variations in worker output can significantly change the actual cost of labor. We need a more thorough approach to accurately estimate labor costs and avoid potential oversights.
3. **Material Costs: A Fickle Factor**: Material prices are very sensitive, which is something to keep in mind for TVC. Changes in supplier deals, shifts in market demand, and even global political situations can cause big changes in the cost of raw materials. This means TVC estimates must be revisited often, because small changes can add up quickly in the overall financial picture.
4. **Economies of Scale: It's Not Always Simple**: While boosting production generally brings down average variable costs per unit, businesses must be aware of potential diminishing returns. There can be a point where more production doesn't lead to a proportionate increase in output, making forecasting TVC more difficult when this aspect is at play.
5. **The Complexity of Multiple Products**: When a company makes a range of products, figuring out the TVC gets much more involved because each product line has its own set of variable costs. Accurate financial analysis requires a more sophisticated approach that's able to properly account for each different cost structure.
6. **The Two Sides of Tech's Impact on Cost**: Introducing new technologies can initially boost variable costs because you have to buy new equipment. However, if done well, these investments can improve efficiency long-term and reduce average variable costs per unit, making the impact of technology on TVC a dual-sided story that needs careful consideration when forecasting.
7. **Seasonal Swings and Their Impact on Costs**: Certain sectors, like farming or retail, have a lot of seasonal variation in demand, and this causes TVC to change predictably. Businesses in these fields need flexible financial plans that account for these fluctuations to manage costs effectively.
8. **Production Design and the Cost Equation**: The design of a company's production process has a big impact on TVC. Processes that are streamlined tend to have lower variable costs because resources are used better and waste is reduced, making efficient engineering a key factor in managing costs.
9. **Hidden Costs: Indirect Variable Costs**: It's easy to forget about indirect variable costs, but overlooking them can make financial analyses less accurate. Things like variable overhead, like the cost of utilities related to production, can influence the overall cost structure.
10. **The Interplay of Suppliers and Variable Costs**: Relationships with suppliers can also introduce 'hidden' variables that aren't usually part of a standard TVC calculation. For instance, if a company relies heavily on one supplier, they might not have as much power to negotiate prices, leading to higher-than-necessary costs. This shows how important it is to have a strategic approach to supplier management in financial forecasting.
Mastering the Formula A Step-by-Step Guide to Calculating Total Variable Cost in 2024 - Practical Examples of Calculating TVC Across Industries
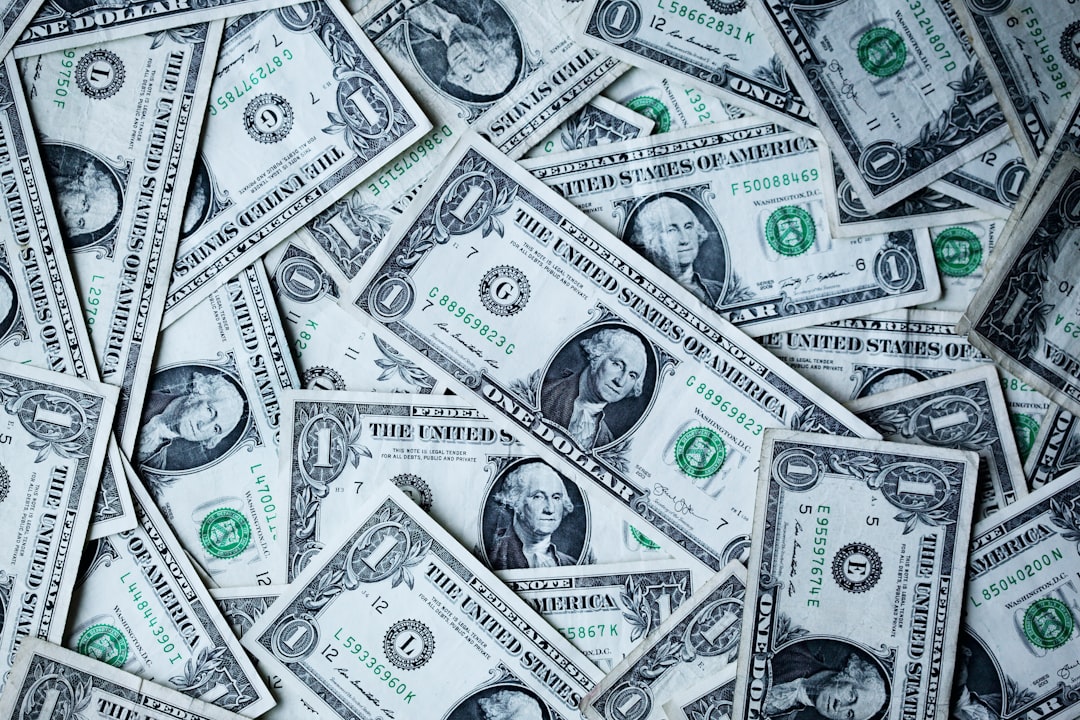
Understanding how Total Variable Cost (TVC) plays out in different industries is key to making good business decisions. Industries like manufacturing, farming, and retail demonstrate how TVC can change a lot based on things like the cost of raw materials, how efficiently workers are doing their jobs, and how demand changes with the seasons. For example, in a manufacturing setting, producing more goods might lead to lower average costs per item thanks to economies of scale. However, in agriculture, how the weather is and the kinds of crops being grown can really impact the total variable costs. By understanding these unique variations, companies can make better plans, adjust their operations, and stay ahead of the competition as the market changes. As we explore more detailed examples, it'll become clear how vital it is to track TVC carefully, especially now that the economy is so complicated and shifting. This is essential for making sure businesses stay in good financial health and grow in the long run.
1. **Healthcare's Diverse Variable Costs**: The nature of variable costs in healthcare is quite complex. A surgery, for instance, involves significantly different material costs compared to a standard outpatient visit. This makes a full picture of TVC hard to pin down and needs to be considered carefully when trying to calculate a business's profitability.
2. **IT Services and Labor Volatility**: For companies providing IT services, labor is often the dominant portion of their variable costs. However, when demand changes quickly, these costs can jump unpredictably due to the need for overtime pay or temporary workers. This highlights how labor costs aren't always stable and require a more detailed examination than basic calculations.
3. **Aerospace's Global Material Dependencies**: In the aerospace industry, the cost of materials like titanium and composites can fluctuate a lot based on the global supply chain. This means aerospace firms need to continually update their TVC calculations since market prices for these components can shift rapidly and dramatically. It's a constant balancing act.
4. **Retail's Holiday Surge**: Retailers regularly see large changes in TVC during holiday seasons as they increase staffing and purchase more promotional inventory. This points to how essential year-round financial planning is for these types of businesses, as simply looking at average costs can miss the large spikes that occur during certain periods.
5. **Food Production and the Weather**: For companies involved in agriculture, TVC isn't just about how much they produce. Weather patterns can have a significant impact on variable costs. Droughts or floods, for example, can severely impact crop yields, potentially leading to substantial changes in expenses due to lost crops or the need to invest in emergency resources.
6. **Craft vs. Mass Production**: When a company uses specialized production methods, the TVC is often higher compared to companies using mass production, due to a higher dependence on skilled workers and specialty materials. If this difference isn't accounted for, it can lead to an underestimation of TVC and skewed financial analyses.
7. **Electronics and Constant Change**: The electronics manufacturing field is characterized by constant technological changes, and these changes can significantly affect variable costs. Firms that adapt quickly can potentially use these advancements to reduce costs, but those who lag behind might face large inefficiencies and higher expenses.
8. **Fashion and Trend Fluctuations**: In fashion, companies need to consider the large fluctuations in TVC associated with fashion trends. These trends create time pressure on production and can affect how accurately the company forecasts costs, potentially requiring more flexible financial models.
9. **Construction's Labor Variables**: The variable costs within construction are largely affected by labor, and that labor cost can fluctuate unexpectedly based on things like union contracts or the specific labor market in the area. These unpredictable cost changes can make it hard to accurately budget.
10. **Utilities in Manufacturing and Usage Intensity**: For manufacturing companies, the costs associated with utilities (electricity, water, etc.) are directly tied to the production intensity. It's essential for manufacturers to keep a close eye on their energy usage to try to avoid unexpected surges in variable costs.
Mastering the Formula A Step-by-Step Guide to Calculating Total Variable Cost in 2024 - Leveraging Technology for Accurate TVC Computations
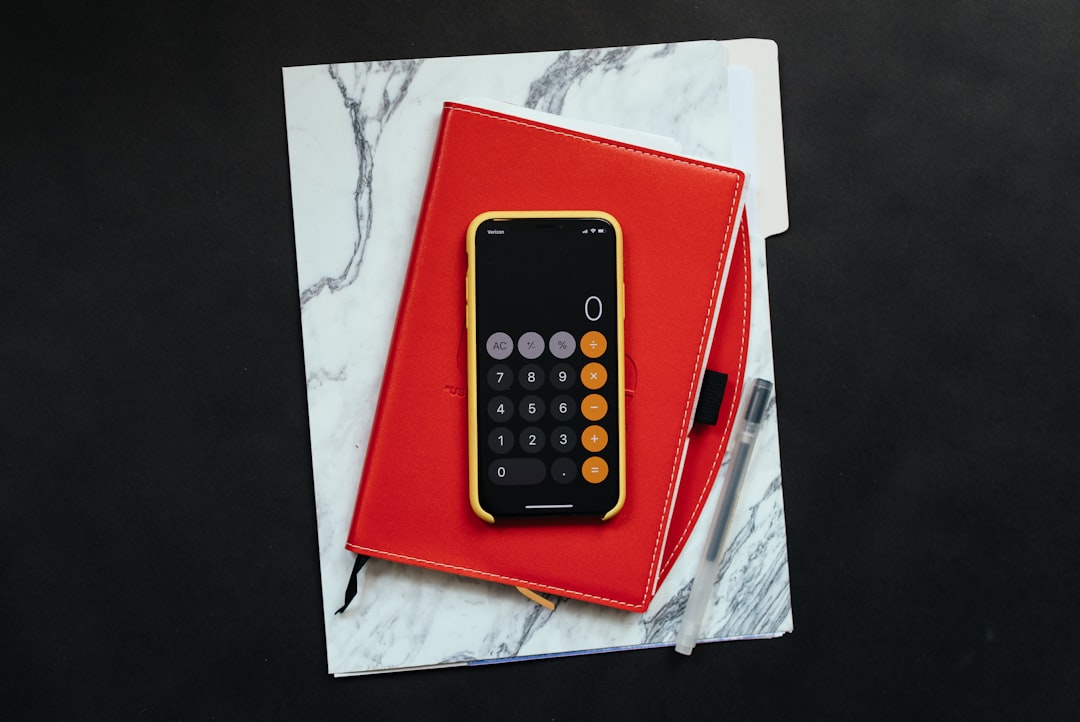
In today's dynamic business environment, utilizing technology for accurate TVC calculations is increasingly vital. Software and tools like advanced analytics, machine learning, and automated systems can improve the precision of TVC calculations by pulling in real-time data on fluctuating costs. These costs include things like raw material prices and changes in labor conditions. While technology can improve efficiency and potentially lower costs over time, its adoption can cause short-term expenses to rise, making TVC assessments more complex. Businesses must remain alert and consistently examine both direct and indirect costs to handle fluctuations in their overall cost structure. The use of technology in business offers both efficiency and added complexity to cost management, and businesses need to carefully track all costs to truly get the most out of technology's benefits.
1. **Predictive Power of Technology**: Using tools like predictive analytics and machine learning can make TVC forecasting much more accurate. These techniques analyze past production data and market trends to help businesses predict changes and adapt their plans accordingly.
2. **Real-Time Cost Tracking**: Modern software can link data from various parts of a business, like purchasing and manufacturing, to give a constantly updated picture of TVC. This quick feedback loop can help avoid the costly delays and errors that are common in older accounting methods.
3. **Blockchain's Transparency**: Using blockchain in supply chains can make tracking the variable costs of raw materials more transparent. Companies can use the clear records provided by blockchain to get more precise TVC calculations and identify any inefficiencies caused by supplier relationships.
4. **AI-Powered Cost Optimization**: Artificial intelligence can be used to automatically monitor resource use and costs, optimizing the efficiency of production. This continuous evaluation can potentially reduce variable costs by minimizing waste and allocating resources more effectively.
5. **Scenario Planning with Simulation**: Simulation software can model how production changes or variations in variable cost components affect the overall costs. This allows companies to see the financial impact of different strategic decisions before making them, resulting in more careful financial planning.
6. **Virtual Production with Digital Twins**: Creating virtual versions of production processes (digital twins) can offer insights into how operational changes affect TVC. Businesses can use digital twins to simulate different scenarios in a virtual environment and spot potential cost-saving opportunities without disturbing real-world operations.
7. **Crowd-Sourced Labor**: In industries with unpredictable demand, using technology to access a wider pool of workers (crowdsourcing) can help manage labor costs. Businesses can change how many workers they need based on real-time production needs, leading to more favorable adjustments in TVC.
8. **Cloud's Impact on Variable Costs**: Cloud computing lets companies scale their IT resources as needed without making large upfront investments in hardware. This reduces fixed costs and can also contribute to more efficient variable cost calculations through easy access to data analytics tools.
9. **IoT and Resource Tracking**: The Internet of Things (IoT) devices can track machinery and resource use in real time, enabling more accurate TVC calculations. Continuous monitoring of variables like energy consumption or material use lets companies adapt operations on the fly.
10. **Standardization Across Operations**: Technology can assist companies with multiple production sites in standardizing their operations and reporting procedures. This can result in more uniform variable costs across different locations, simplifying the calculation and analysis of total variable costs company-wide despite geographic differences.
Mastering the Formula A Step-by-Step Guide to Calculating Total Variable Cost in 2024 - Applying TVC Insights to Strategic Decision-Making in 2024
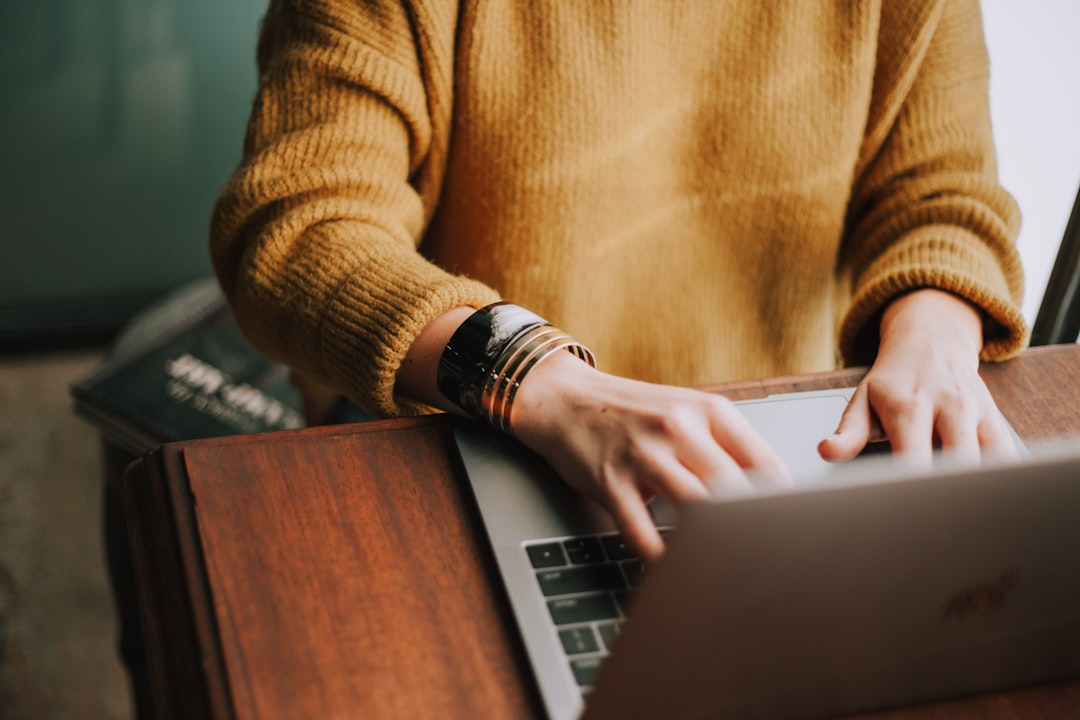
In the dynamic business environment of 2024, understanding and applying insights derived from Total Variable Cost (TVC) is crucial for strategic decision-making. By harnessing data-driven insights, businesses can refine their goals, pinpoint areas where they can boost efficiency, and distinguish between realistic and impractical objectives. Given the need for quick decision-making in today's world of frequent disruptions, comprehending a business's cost structure through TVC is becoming increasingly important. Moreover, fostering a company culture where data analysis is valued can help lessen biased decisions and expose hidden patterns that could lead to fresh strategic possibilities. As businesses continue to navigate an uncertain world, effectively using TVC insights has become a vital component of informed, adaptable leadership. While the concept of TVC itself is not new, its strategic application in this context of rapid change and readily available data presents fresh challenges and opportunities.
1. **Blending TVC with Predictive Insights**: We're seeing a growing trend in 2024 where firms are using predictive analytics alongside TVC insights to anticipate future costs and production requirements. This proactive approach, rather than a reactive one, is helping make better decisions overall. It's intriguing how combining these two aspects can give a clearer picture.
2. **The Challenge of Variable Costs**: Recent research suggests that around a quarter of businesses aren't properly accounting for cost changes due to shifts in the market. Failing to account for these variations in TVC calculations can lead to substantial financial errors and poor strategic choices. It's concerning how often this seems to be overlooked.
3. **Technology's Costs**: Introducing cutting-edge manufacturing technologies might lead to an initial increase in TVC due to setup and training expenses. But it's important to remember the long-term picture, as efficiency gains should, eventually, decrease costs. It makes me wonder how firms are strategizing these transitions effectively.
4. **Comparing Costs Across Industries**: Each industry has its own set of benchmarks for TVC. For example, tech companies often see variable costs heavily impacted by R&D, while traditional manufacturing is usually more focused on fluctuating material and labor costs. It's interesting to compare how different fields grapple with managing variable costs.
5. **Labor's Role in TVC**: In many engineering fields, a significant portion of variable costs (around 40%) are connected to labor, including overtime and specialized training. This makes it crucial to have very precise estimates for labor costs in TVC calculations to avoid major errors. It's striking how important a seemingly 'simple' factor like labor can be in the bigger cost picture.
6. **Global Currency's Impact**: Businesses involved in international supply chains have to factor in currency changes when calculating TVC, especially when materials are sourced from different countries. Understanding these complexities is essential for keeping costs accurate. It's quite complex to untangle the various influences on variable costs.
7. **Seasonality's Effect on Profits**: Analyzing how seasonal demand shifts affect TVC reveals that failing to adjust those calculations can cause up to 15% variance in expected profits during peak periods. This really highlights the need for flexibility in planning. It's interesting how these seemingly minor adjustments can have a larger impact.
8. **Tracing Costs**: Firms are increasingly using advanced algorithms to better track and assign indirect variable costs. This leads to a more precise understanding of overall TVC. It's impressive how technology is helping tease apart more nuanced cost structures.
9. **Supplier Relationships and Costs**: Research suggests that businesses with solid supplier relationships can experience lower variable material costs (10-15%). This really emphasizes the financial value of strategic partnerships. It's intriguing how such relationships can result in such tangible cost savings.
10. **Regulatory Changes and Costs**: New regulations across industries can create new variable costs, making it essential for businesses to keep an eye on these changes and adjust TVC calculations accordingly. It's important to consider how regulations create shifting costs, and it would be fascinating to analyze this across various industries.
More Posts from mm-ais.com: